In the ever-evolving world of industrial components, the 1 4 flange holds a critical place due to its versatility and essential role in various applications. These flanges are frequently used in piping systems, contributing significantly to connecting pipes, valves, and other equipment. Understanding the nuances of this component can help industries optimize their operations, reduce maintenance costs, and improve systems' durability and efficiency.
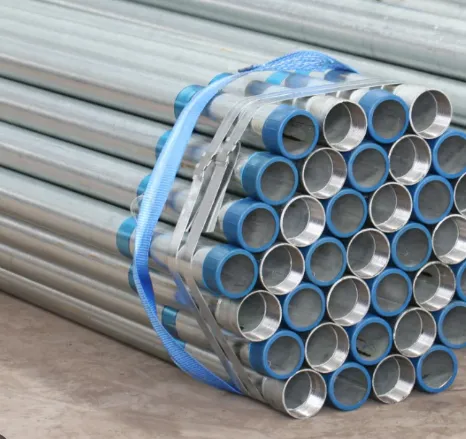
Real-World Application and Experience
Flanges are indispensable in many sectors, such as oil and gas, chemical manufacturing, water treatment, and power generation. The 1 4 flange size offers a practical solution for systems that require moderate flow and pressure management. Based on firsthand experience in the field, these flanges have shown exceptional reliability in mid-size piping systems, where space constraints necessitate compact yet sturdy components.
A notable experience includes their application in chemical processing plants, where the precision of the 1 4 flange helps prevent leaks and withstands high pressure and temperature variations. Engineers have often integrated these flanges into heat exchangers and pump systems, utilizing their precise metal-to-metal seal to avoid potential system failures, thereby guaranteeing uninterrupted operations.
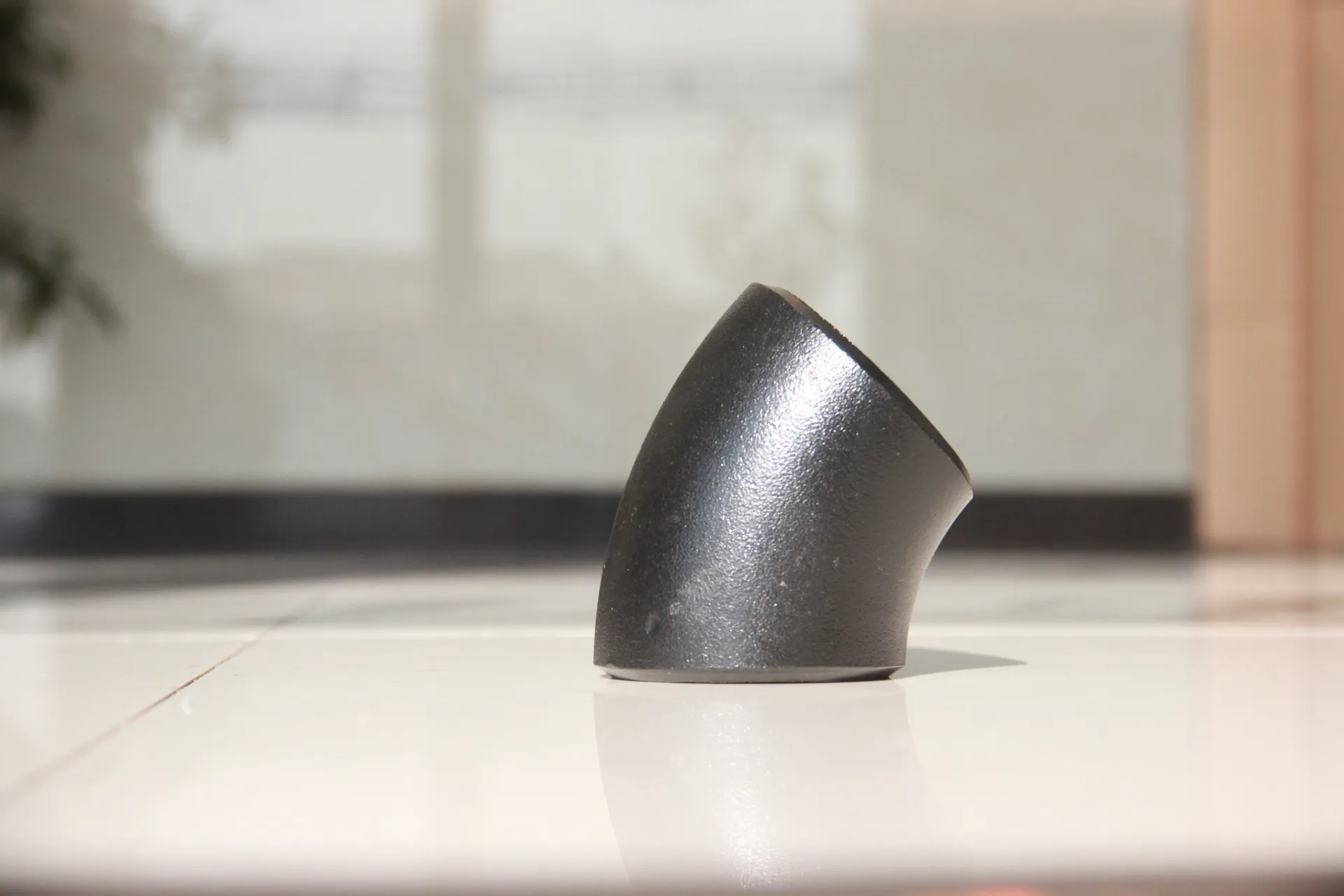
Expertise and Technical Specifications
From a technical standpoint, 1 4 flanges come in various materials such as stainless steel, carbon steel, and alloy steel, each chosen based on the specific application requirements such as resistance to corrosion or thermal stability.
These flanges are manufactured in compliance with industry standards like ASME B16.5, ensuring they meet safety and quality thresholds essential for maintaining system integrity.
The 1 4 flange is typically available in different types, including slip-on, weld neck, socket weld, and threaded options, allowing for adaptability across different joint types and installation preferences. Each type offers distinct advantages, such as the ease of installation with slip-on flanges or the enhanced strength provided by weld neck flanges.
1 4 flange
Authoritativeness in the Industry
The authoritative selection of a 1 4 flange is crucial for project success. Top manufacturers like Anvil International, Parker Hannifin, and Eaton play significant roles in producing high-quality flanges. These companies leverage advanced manufacturing technologies and stringent quality control processes to deliver products that not only comply with international standards but also provide unmatched durability and performance.
Alongside these manufacturers, industry bodies such as the American Petroleum Institute (API) and the International Organization for Standardization (ISO) help establish guidelines that ensure these components can reliably perform in demanding environments. The trust that these authoritative entities provide reinforces the critical importance of choosing the right flange for specific engineering needs.
Trustworthiness and Best Practices
Selection of the appropriate 1 4 flange requires a thorough understanding of the operational environment and expected performance criteria. Factors such as pressure class, temperature range, and exposure to corrosive elements must be considered to ensure the longevity and effectiveness of the flange in service. Consulting with experienced engineers and utilizing simulation tools to predict performance under various conditions can enhance decision-making and build confidence in the selected flange solution.
Moreover, regular maintenance and inspection are essential for sustaining the trustworthiness of flange connections. Implementing a proactive maintenance schedule that includes visual inspections for wear and tear, periodic pressure testing, and corrosion inhibitor applications can extend the lifecycle of these critical components.
In conclusion, the 1 4 flange emerges as a vital component in diverse industrial applications, valued for its adaptability, reliability, and compliance with rigorous standards. By leveraging reputable manufacturers, adhering to best practices, and drawing on real-world experiences, industries can assure optimal performance and bolster the trust that stakeholders place in their systems. As advancements in materials and manufacturing technologies continue to evolve, the future of flange applications promises even greater efficiency and reliability, ensuring they remain a cornerstone of industrial fluid handling systems.