In the industrial manufacturing and construction sectors, the term 1 inch flange surfaces frequently, highlighting its significance as a vital component in various applications. These small yet mighty components serve as essential connectors to join pipes, valves, pumps, and other equipment, ensuring the seamless flow of liquids and gases. This article delves into the practical experience, technical expertise, authoritative sources, and reasons for trust regarding 1 inch flanges.
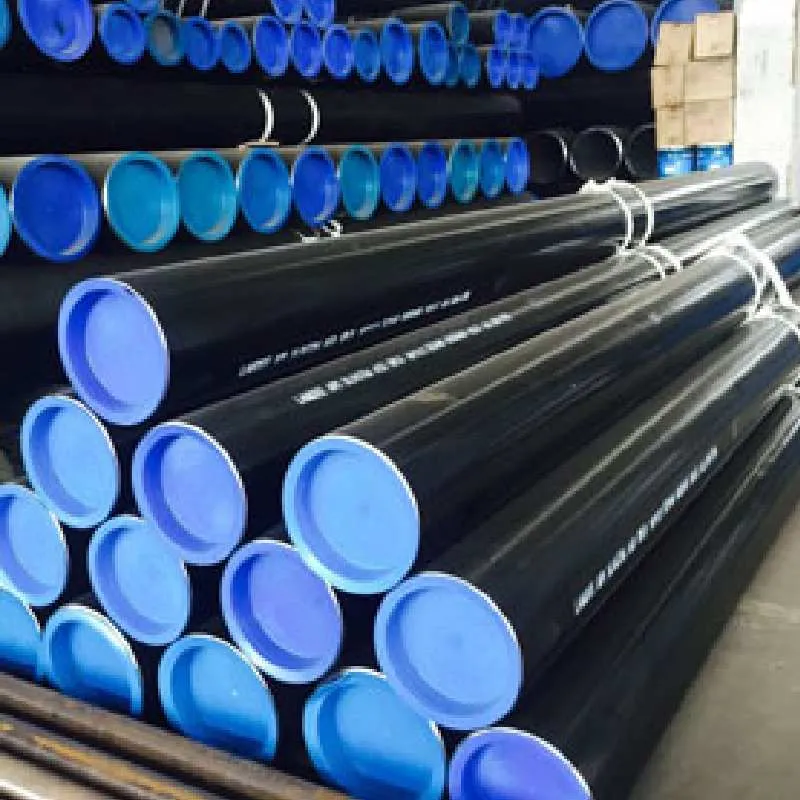
The journey to understanding 1 inch flanges begins with acknowledging their scope of application. These flanges are often seen in industries such as petrochemical, oil and gas, water treatment, and HVAC systems. Their utility stems from their adaptability to different pressure ratings, commonly found in ANSI, DIN, and JIS standards, to name a few. Their versatility allows them to perform under varying conditions, making them invaluable to projects demanding a robust and reliable connection.
Expertise in flanges underlines the importance of selecting the right type based on the application. When dealing with 1 inch flanges, it is crucial to assess the type weld neck, slip-on, socket weld, lap joint, screwed, or blind. Each type offers its unique advantages; for example, the weld neck flange is designed to provide high integrity in severe service conditions, where vibration and high pressure are prevalent. Meanwhile, the slip-on flange is easy to install and suitable for low-pressure applications. Thus, knowledge about these types facilitates informed decisions, contributing to the safety and efficiency of operations.
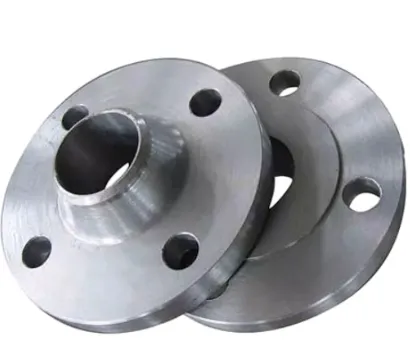
Authoritativeness in the realm of flanges can be demonstrated by reference to regulatory standards, which dictate manufacturing specifications and quality benchmarks. Reputable organizations such as the American Society of Mechanical Engineers (ASME) and the International Organization for Standardization (ISO) provide guidelines and certification to ensure flanges meet rigorous quality and safety standards. Additionally, ASTM International, a revered authority, contributes to testing and material specifications that enhance the reliability of these components.
1 inch flange
In terms of material consideration, 1 inch flanges are commonly manufactured from stainless steel, carbon steel, and alloy steel.
The choice of material impacts the durability and corrosion resistance of the flange. For instance, stainless steel flanges are favored in environments exposed to moisture due to their rust-resistant properties, offering longevity and reducing the need for frequent replacements.
Trustworthiness in any industrial product boils down to its performance and reliability, bolstered by rigorous testing and real-world applications. Testimonials and case studies from leading companies and industry veterans often highlight the practical applications of 1 inch flanges under challenging conditions. Their stories provide real-world validation of their functionality and reliability, corroborating trust in these components.
To sum up, the 1 inch flange plays a critical role in ensuring seamless connectivity between various components in industrial systems. Drawing from hands-on experience and vast knowledge allows for appropriate selection, while adherence to strict standards ensures quality and performance. With authoritative bodies backing their specifications and real-world applications validating their integrity, these flanges have earned trust across the industries they serve. This multifaceted understanding underscores why the 1 inch flange remains a cornerstone in industrial applications, seamlessly integrating with complex systems and ensuring operational excellence.