In the world of industrial construction and piping, the 2 1 2 flange serves as a critical component that bridges connects, or terminates pipes in a wide array of applications. Its importance cannot be overstated, and understanding its nuances can tremendously enhance operational efficiency and safety in pipeline systems.
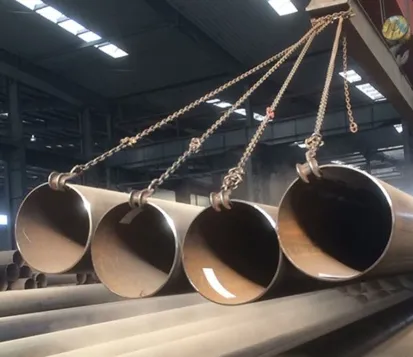
The 2 1 2 flange, typically indicating a 2 1/2-inch size, is used extensively in industries such as oil and gas, water treatment, and petrochemicals. It performs the crucial function of allowing for the easy assembly and disassembly of piping systems—facilitating maintenance, inspections, repairs, and the reconfiguration of pipelines. The flexibility and practicality this component offers make it indispensable in various sectors.
One of the primary materials used in the manufacturing of 2 1 2 flanges is stainless steel, prized for its exceptional resistance to corrosion, heat, and chemical exposure. Other materials include carbon steel, alloy steel, and sometimes exotic alloys for specialized applications. The choice of material is critical, dictated by the specific requirements of the service conditions such as temperature, pressure, and corrosive environment.
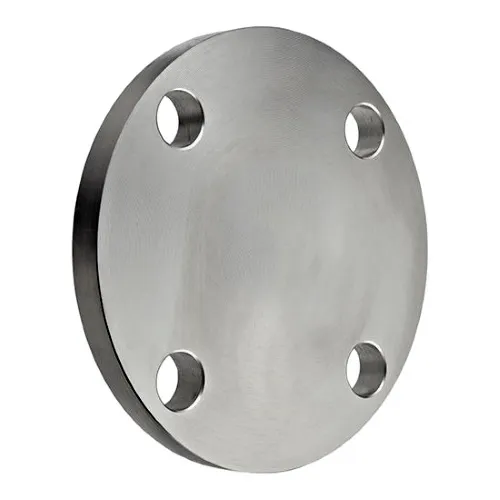
Several types of flanges fall under the 2 1 2 category, including welding neck, slip-on, socket weld, lap joint, and threaded, each designed to meet specific needs and operational requirements. For instance, a welding neck flange, characterized by a long tapered hub, is typically used in high-pressure scenarios, whereas slip-on flanges are preferred for lower-pressure applications due to their simplicity and ease of use.
Expertise in selecting the correct type of 2 1 2 flange is essential for ensuring system performance and integrity. Engineers often rely on industry standards outlined by organizations such as the American National Standards Institute (ANSI), the American Society of Mechanical Engineers (ASME), and the International Organization for Standardization (ISO) to ensure that flanges meet the necessary specifications for safety and performance.
Proper installation and maintenance of 2 1 2 flanges are critical to their function. Ensuring precise alignment, employing appropriate bolting sequences, and adequate torque application are essential steps for effective installation. Incorrect installation can lead to failures, resulting in costly downtime and safety hazards.
In addition to the installation, the longevity and reliability of 2 1 2 flanges are heavily dependent on maintenance practices. Routine inspections should include checks for leaks, corrosion,
and signs of wear or damage. Advanced non-destructive testing techniques like ultrasonic testing and radiographic testing can provide insights into the integrity of the flange without disrupting operations.
2 1 2 flange
The innovation in flange technology is evolving with the integration of advanced materials and manufacturing techniques. 3D printing and additive manufacturing, for instance, are making it feasible to produce flanges with enhanced properties tailored to specific applications, potentially leading to even greater reliability and performance.
A significant aspect of using 2 1 2 flanges lies in ensuring trust and compliance with safety regulations and industrial standards. This requires sourcing flanges from reputable manufacturers who adhere to strict quality control measures, often substantiated by third-party certifications.
For those operating in environments where failure is not an option, such as nuclear power plants or offshore drilling platforms, the authority of the flange's design and the trustworthiness of its manufacturer cannot be compromised. Consulting with experienced engineers and material scientists is often necessary to choose the ideal flange for critical applications.
Real-world applications demonstrate the vast potential and critical nature of the 2 1 2 flange. For example, in the petrochemical industry, where the safe transport of volatile substances is paramount, the robustness of flange connections can prevent catastrophic spills and ensure smooth operations.
For any company seeking to build or maintain a high-performance piping system, investing in high-quality 2 1 2 flanges and collaborating with professionals who possess extensive expertise in this domain is vital. It not only enhances the operational efficiency but also fortifies the trust and reliability of the system—a non-negotiable requirement in today's competitive and safety-conscious industrial landscape.
In conclusion, the 2 1 2 flange represents more than just a hardware component; it embodies a crucial intersection of engineering expertise, safety assurance, and material science. By adhering to best practices and leveraging the latest technologies, industries can maximize their system's reliability and safety, ultimately building a reputation for excellence and dependability in their respective fields.