The world of plumbing and fluid engineering often hinges on the critical components that ensure seamless and leak-free connections. Among these, the 2 inch pipe flange stands as a cornerstone, providing robust solutions in various industrial applications. Understanding its importance, application, and selection criteria is crucial for professionals committed to high-performance and efficient systems.
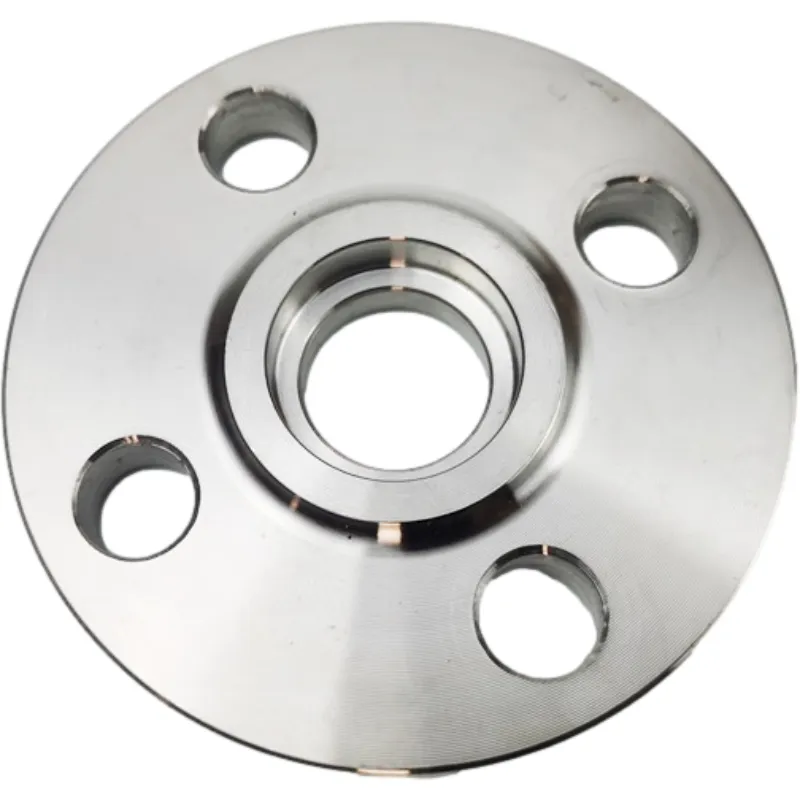
A 2 inch pipe flange is instrumental in connecting pipes, valves, pumps, and other equipment to form a piping system. Its primary function is to offer flexibility in maintenance, easy assembly in confined spaces, and the potential for modification of the system. The range of materials available for pipe flanges, including carbon steel, stainless steel, and various alloys, ensures suitability across different environments and pressures.
The application of a 2 inch pipe flange spans across both domestic and industrial sectors. In industrial settings, where the management of gases and liquids is key, flanges ensure that connections can be made and dismantled with minimal risk of leaks. This is particularly vital in high-pressure conditions such as oil and petrochemical industries where flange joints must withstand significant stress. Moreover, in fluid transportation systems, the role of pipe flanges becomes even more pronounced. They allow for the accommodation of thermal expansion and can help manage vibration and shock loads, thereby protecting the integrity of the entire pipeline system.
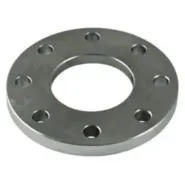
Selecting the right flange requires a comprehensive understanding of several factors, including the pressure and temperature conditions, the material's corrosion resistance, and the flange's mechanical strength.
For a 2 inch flange, the pressure class (Class 150, 300, 600, etc.) must correspond to the application's maximum pressure rating. Understanding ASME/ANSI standards that govern flange specifications is critical for ensuring compatibility and safety.
Furthermore, innovations in flange technology have introduced advanced features. For instance, the incorporation of raised faces in flanges has improved sealing capabilities. The specific design, known as the raised face flange, is often employed where higher pressure ratings are required. This design increases the capability of the flange to distribute pressure across the sealing surface more efficiently, reducing the risk of gasket blowouts and leaks.
2 inch pipe flange
When it comes to installation and maintenance, experience plays a vital role. Ensuring that the flange is properly aligned and bolted with the correct torque is essential to prevent misalignments that might cause undue stress on pipelines. Regular maintenance checks are required to inspect for signs of wear, corrosion, or any mechanical damage that could compromise the system's integrity.
From an expertise standpoint, knowledge in the latest engineering standards and practices can elevate the use of a 2 inch pipe flange. This includes understanding the role of companion flanges, flanged fittings, and the variances in flange face designs, such as slip-on, socket weld, and lap joint flanges. Each type offers specific advantages depending on the pipes' material and endpoint connection requirements.
Incorporating trustworthiness, suppliers and manufacturers of pipe flanges often provide material test reports (MTRs) and compliance certifications which should be scrutinized for authenticity. Engaging with reputable vendors adds a layer of security knowing that the components meet specified industry standards.
In conclusion, the 2 inch pipe flange is not merely a connector but a pivotal element in engineered systems that require reliability and flexibility. With technological advancements and growing demands across industries that handle fluid and gas transportation, the meticulous selection and application of these components cannot be understated. Leveraging professional expertise, adhering to stringent standards, and remaining vigilant in maintenance practices enrich the value and longevity of piping systems. For professionals across engineering fields, mastery over the nuanced aspects of pipe flanges is indispensable, enhancing operational efficiency and sustaining the safety of critical infrastructure projects.