Understanding the diverse range of flange types is essential for industries that rely heavily on pipelines and connected systems. These crucial components are pivotal to maintaining the integrity and functionality of various infrastructures, whether in petrochemical plants, natural gas distribution networks, or water treatment facilities. Common flange types cater to distinct applications and specific engineering requirements, each possessing unique characteristics that render them suitable for particular operational conditions.
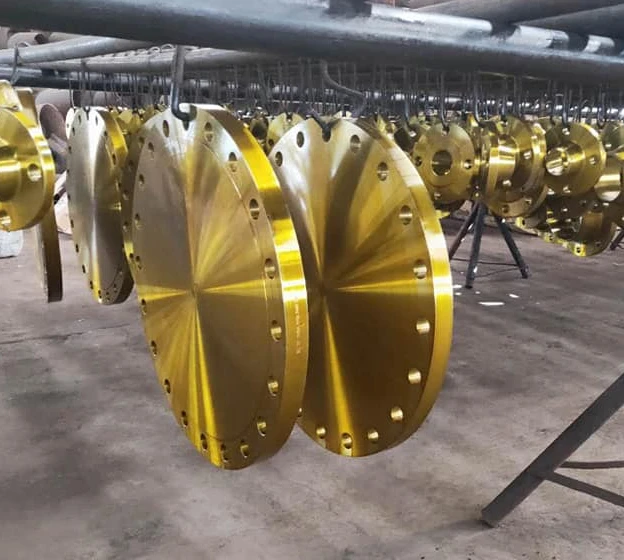
One of the most prevalent flange types is the Weld Neck Flange. Known for its robust construction and ability to withstand extreme pressure and temperature variations, the weld neck flange is distinguished by its tapered hub and butt-welded connection. This design optimally distributes stress through the pipeline, reducing the potential for turbulent flow and erosion within the system. Utilized extensively in high-pressure environments, such as in oil and gas industries, the weld neck flange’s durability ensures long-term operational safety and efficiency.
Slip-On Flanges, alternatively, offer a simpler and more cost-effective solution. Their name derives from the fact that they slip over the pipe, and only minimal welding – on the inner and outer side of the flange – is required to secure them in place. While they may not match the weld neck flanges in terms of strength, slip-on flanges are easier to align. This ease of installation makes them ideal for low-pressure applications where frequent disassembly and maintenance might be necessary, manifesting their utility across various industries like HVAC systems and plumbing works.
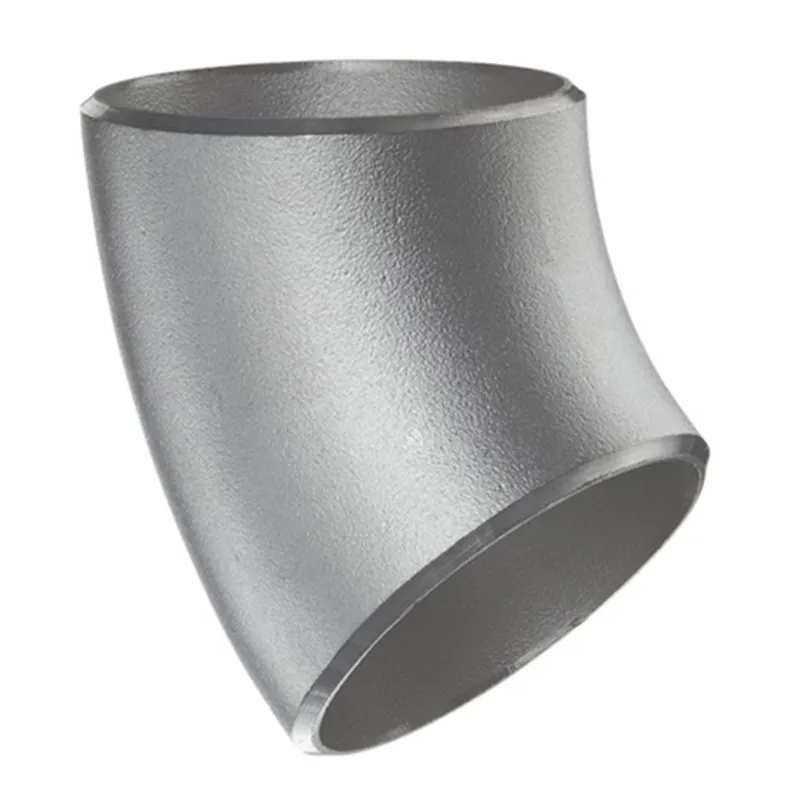
For scenarios demanding exceptional sealing to prevent leakage, Blind Flanges are indispensable. These flanges do not possess a bore and are used to seal the end of a piping system or valve, effectively blocking off certain sections for maintenance or the rerouting of flow. Their simplicity does not undermine their contribution; blind flanges are vital for ensuring the safety and operability of pipeline systems, especially when system modifications are frequent.
Threaded Flanges provide an innovative alternative, particularly for operations where welding is undesirable or impossible. These flanges feature a bore with threads, allowing them to be screwed onto a matching pipe, thus facilitating rapid and secure installations. They are particularly beneficial in high-risk environments where heat and sparks from welding pose safety concerns, such as in potentially explosive atmospheres within refining operations or mining activities.
common flange types
Socket Weld Flanges are another type that demands attention, primarily used in smaller size high-pressure piping. These flanges allow the pipe to be inserted into a recessed area of the flange before being secured with a fillet weld. This design is adept at minimizing residual stress at the weld site, consequently reducing the risk of thermal fatigue. Industries dealing with high-stress environments or corrosive substances, like chemical processing, often rely on the precision and secure fittings of socket weld flanges.
Lap Joint Flanges are also noteworthy due to their utility in systems requiring frequent disassembly for inspection, cleaning, or maintenance. They comprise two components a stub end – which is butt-welded to the pipe, and the loose backing flange that can be rotated around the stub end for alignment purposes. This configuration eases installation in complex systems with space constraints, highlighting its value in industries like shipbuilding and food processing.
The selection of the appropriate flange type is a decision that must be grounded in comprehensive technical analysis and operational foresight. Each flange's specifications, such as material composition, size, pressure rating, and operational environment, must be finely scrutinized to ensure conformity with engineering standards and regulatory requirements.
Integrating expert knowledge and operational insights is paramount. Experts in the field maintain that understanding the nuanced performances of each flange type against specified criteria can drastically influence system longevity and reliability. Leveraging advancements in flange designs, materials, and manufacturing processes is central to enhancing adaptability and resilience in modern industrial operations.
In conclusion, while choosing the right flange type might seem like a straightforward task, it encompasses intricate considerations that directly impact system performance and safety. By recognizing the specific strengths and limitations of common flange types and aligning them with precise operational demands, industries can achieve optimized functionality and enhanced operational safety, ultimately securing their technological edge in a competitive market landscape.