Flanges are integral components in piping systems, serving to connect pipes, valves, pumps, and other equipment to form a secure and accessible configuration. Understanding the different types of flanges and their specific applications is vital for ensuring system efficiency and safety. The selection of flanges depends on several factors such as pressure and temperature range, pipe size, and material compatibility. Here, we delve into the most commonly used types of flanges in piping, illustrating their essential roles and contributions to successful piping projects.
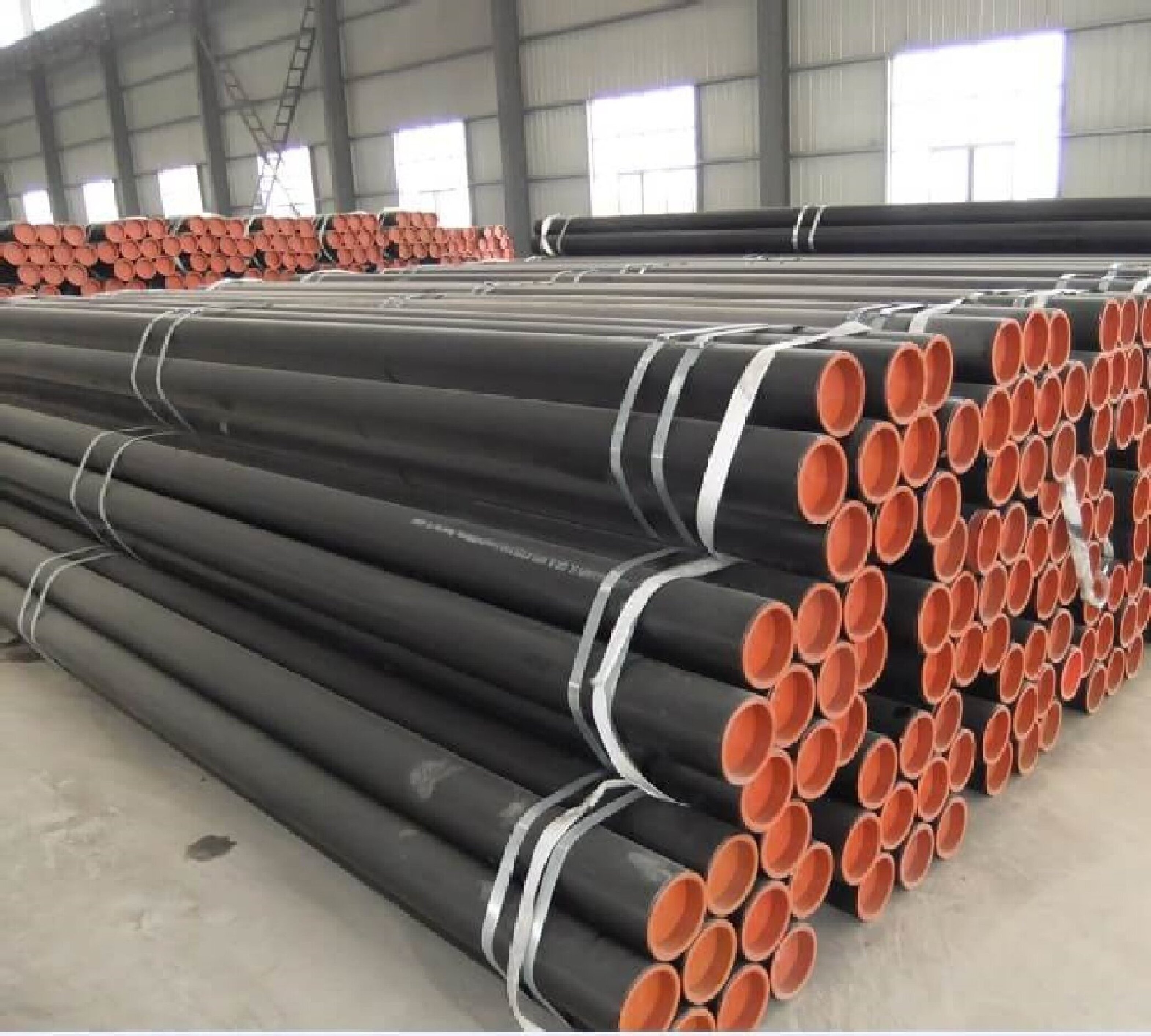
1. Weld Neck Flange
Highly favored for high-pressure environments, weld neck flanges are characterized by their long-tapered hub. This design integrates the flange with the pipe, thus offering strength and reducing stress concentration at the base of the flange. These flanges are ideal for severe conditions such as extreme temperature fluctuations and pressure changes. Due to their formidable resistance and durability, these are often recommended in refineries and petrochemical industries where performance cannot be compromised.
2. Slip-On Flange
Slip-on flanges are easier to install compared to other types, as they slide over the pipe. They are welded both inside and outside to provide sufficient strength preventing leakage. While less robust than weld neck flanges, slip-on flanges are used widely for lower pressure applications and non-critical scenarios where ease of replacement is a priority. Their affordability and simplicity make them suitable for water pipelines and various mechanical systems where conditions are moderate.
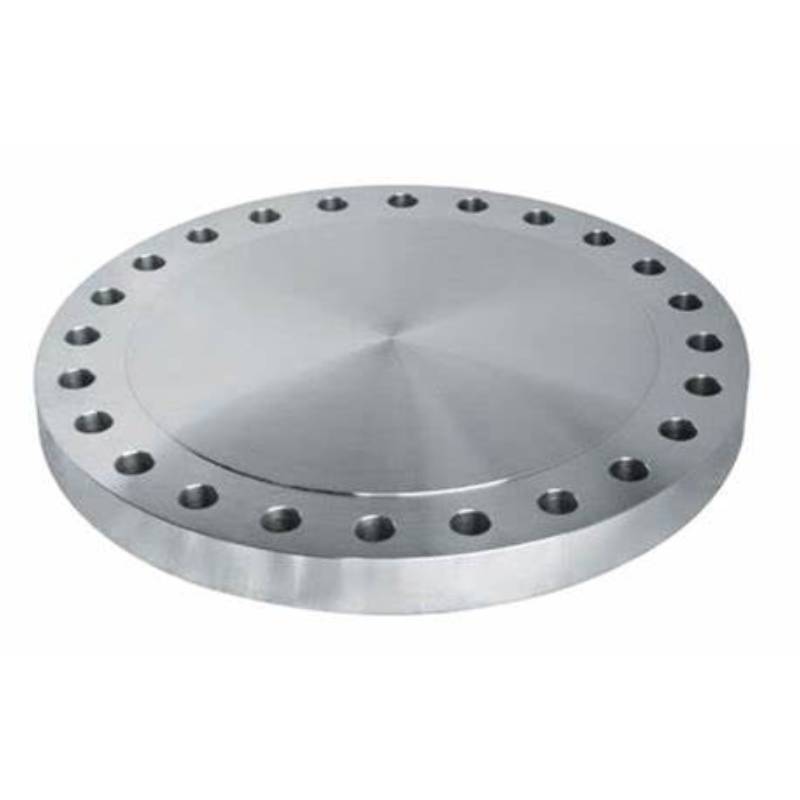
3. Socket Weld Flange
These flanges are employed typically in high-pressure systems of small diameter pipes. The pipe is inserted into the socket end and fillet welded around the top. This ensures a smooth bore and better flow of the medium inside the pipe. The excellence in fatigue resistance suits them for plumbing systems and gas pipelines, particularly in cases where small diameters and high pressure are involved.
4. Blind Flange
An essential type used to terminate pipelines, valves, and openings in a system, blind flanges do not have a bore and are often used for isolation and pressure testing. Ensuring complete stoppage of flow, blind flanges are crucial for maintenance works by allowing sections of the pipeline to be efficiently shut. They are reliable pressurers and exhibit excellent mechanical performance when installed in pipelines dealing with corrosive or hazardous substances.
different types of flanges used in piping
5. Lap Joint Flange
Used in conjunction with a stub end, the lap joint flange freely rotates around the stub end. This posits a significant advantage in scenarios where frequent alignment or disassembly is required. In systems demanding regular inspection or containing materials that require continual updates, lap joint flanges offer flexibility. However, they are not generally used where the system involves high pressure and extreme temperature changes due to their fair seal capability.
6. Threaded Flange
Threaded flanges are unique as they do not require welding, making them appealing for small diameter, low-pressure applications. They are easy to assemble and ideal for situations where welding is not feasible, such as in explosive atmospheres where high temperature-based operations are restricted. Their disadvantage in terms of unsuitability for large diameters and pressures is made up by their simplicity and adaptability in various minor systems and temporary connections.
7. Orifice Flange
Engineered for flow measurement, orifice flanges feature orifice plates and pressure tap connections. These are primarily used in industries requiring precise flow data within the system, such as in chemical plants where processes need meticulous monitoring. The integration of orifice plates with the flange streamlines the method of gauging flow rates, letting engineers modify process parameters rapidly and efficiently.
Incorporating the right type of flange ensures a well-functioning, robust pipeline system. Expert knowledge of materials and environmental conditions, combined with engineering acumen, guides the optimal selection and application of the right type of flange. Professionals in the field must remain abreast of industrial standards and technological advancements to employ flanges that assure reliability, safety, and performance excellence in their specific engineering contexts.