In the realm of industrial piping and engineering, DIN (Deutsches Institut für Normung) flanges play a critical role in ensuring seamless connections and optimal flow within complex systems. As the premier German standard, DIN flanges have carved their niche in global markets, necessitating a deep dive into their types to better understand their applications, benefits, and standards.
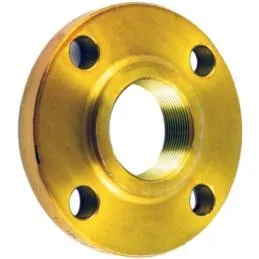
DIN flanges are recognized for their precision and solid engineering principles, making them indispensable in industries where reliability and safety are paramount. Among the myriad types of DIN flanges, each serves a specific function in the management and conveyance of fluids.
Here is an insight into some of the most prevalent types
1. DIN 2633 – This flange type is widely used in moderate pressure systems and is constructed to handle up to PN 16 pressure class. It finds its applications predominantly in the chemical and petrochemical industries. Its robustness ensures a tight seal, critical for maintaining integrity in fluid handling processes.
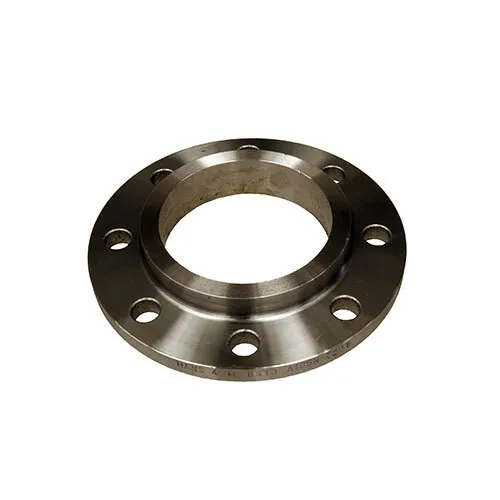
2. DIN 2576 – Classified under the PN10 pressure rating, these flanges are typically used in low-pressure systems. Their design renders them ideal for water and wastewater management systems where pressure demands are not as high, yet efficiency and durability remain necessary.
3. DIN 2642 – A variant primarily used in piping systems requiring frequent assembly and disassembly, such as in maintenance operations. They operate under the PN 16 category and are known for their resilience in systems needing extensive upkeep, maintaining both cost and time efficiency.
4. DIN 2527 – These are blind flanges, critical for terminating piping systems and conducting inspections. These flanges are invaluable in systems where expansion might be anticipated. Their strength and reliability are crucial in ensuring complete containment of fluids within the system.
5. DIN 2674 – Also coming under a lower pressure class, these flanges are suitable for lightweight industrial applications. The design facilitates adequate performance without the overengineering that might be unnecessary in less demanding systems.
din flange types
The selection of a specific flange type hinges upon several factors such as the nature of the fluid, the operating temperature, and the pressure conditions. DIN standards ensure that each flange not only meets stringent quality criteria but also fits seamlessly into various industrial setups, minimizing the risk of leaks and system failures.
One of the crucial advantages of DIN flanges is their versatility and the ease with which they can be customized to meet specific industrial needs. This adaptability is bolstered by a robust quality assurance process that guarantees performance across diverse operating conditions, making them a trusted choice for engineers worldwide.
In terms of material composition, DIN flanges are available in various materials including stainless steel, carbon steel, and specialized alloys. The choice of material significantly influences the flange's resistance to corrosion and temperature, thus impacting its suitability for different industrial environments.
Moreover, DIN flanges offer the flexibility of being integrated seamlessly with international standards, such as ANSI or JIS, thereby expanding their applicability in multi-national projects and systems. This compatibility further enhances their authority on a global scale, promoting trust and dependability.
Therefore, when considering DIN flanges for your industrial applications, it's imperative to consult with professionals who possess the expertise and experience in the field. They provide actionable insights derived from a profound understanding of both the technical and practical aspects, ensuring that the chosen solution delivers exceptional performance and reliability in line with expectations.
In sum, DIN flange types are more than mere components; they are vital to the seamless operation of modern industrial systems. Their precision engineering reflects the expertise imbued in every flange, affirming their position as a cornerstone in achieving operational excellence.