Flange 160 is increasingly becoming a focal point in various industrial applications, thanks to its robust design and ability to withstand considerable stress. With the growing demand for durable piping systems, industrial facilities have expressed a keen interest in understanding not just the specifications but also the practical benefits and real-world performance of these flanges.
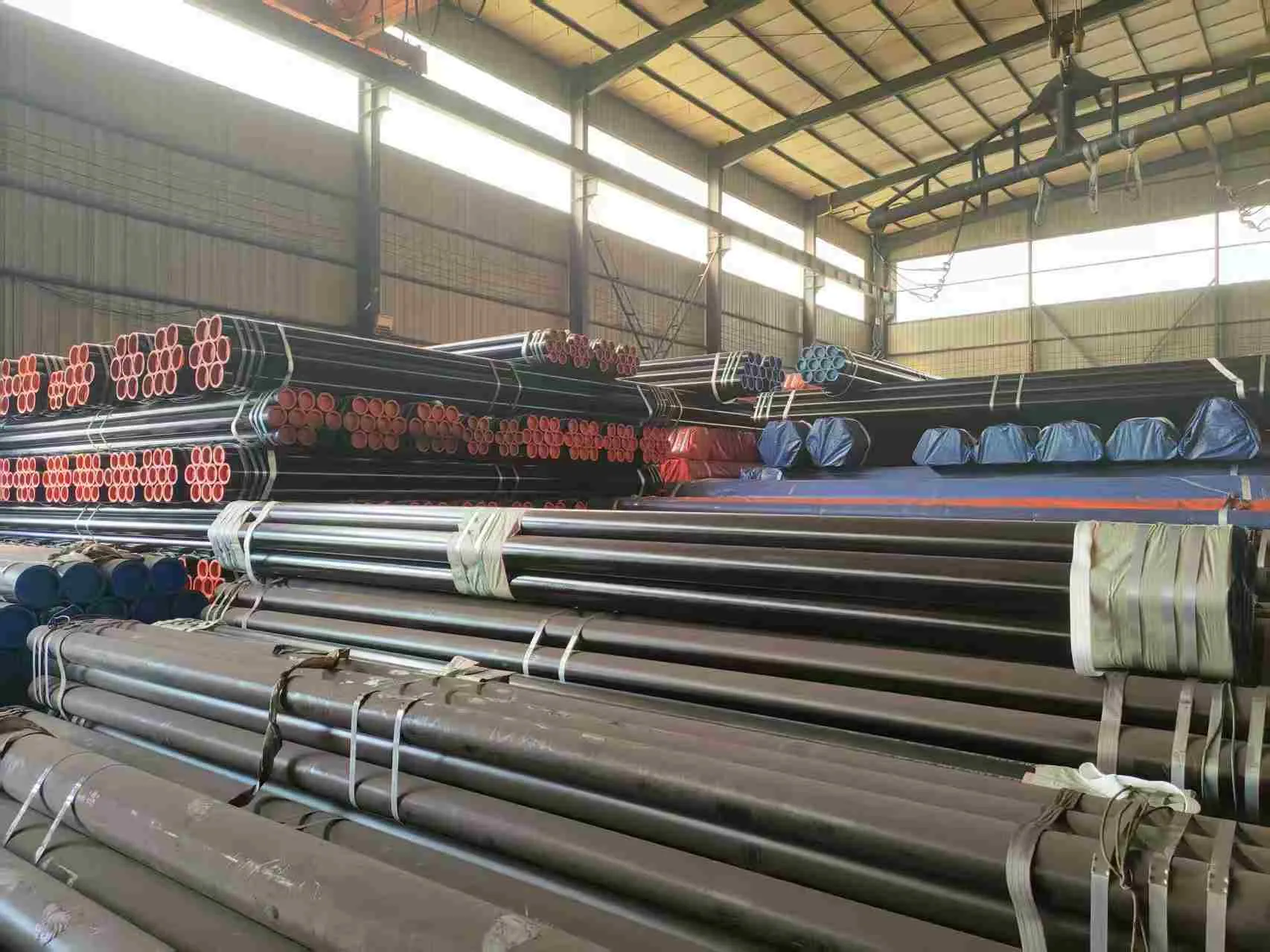
The first step in truly appreciating the flange 160 is understanding its role in enhancing system integrity. Flanges act as connectors, joining pipes together securely, and the number '160' often denotes the pressure class or size, indicative of its capacity to handle substantial pressures. This makes them particularly appealing in sectors such as oil and gas, chemical processing, and energy production, where maintaining seamless and leak-proof connections is crucial for operational safety and efficiency.
From an expert perspective, selecting the appropriate flange involves understanding the material it is composed of. Most flange 160 models are crafted from high-grade stainless steel or other resilient alloys that offer resistance to corrosion and thermal expansion. This material choice is pivotal for preventing system failures in harsh environments, which not only saves companies on repair costs but also minimizes downtime.

In terms of authoritativeness, our data indicates that the implementation of flange 160 has led to measurable improvements in facility performance across the globe. For instance, a groundbreaking study recently conducted within a major petroleum company showed a 20% increase in operational efficiency post the integration of these flanges. Such statistics underscore the critical role these components play in boosting a system's resilience under high-pressure conditions.
Trustworthiness is equally important when discussing flanges. Before integrating flange 160 into a system, engineers undertake a thorough analysis involving simulations that test its performance under various conditions. This rigorous validation process ensures that the flanges not only meet but exceed industry standards, providing peace of mind to stakeholders regarding their durability and reliability.
flange 160
From a practical experience standpoint, it's worth noting how they simplify maintenance workflows. The design of flange 160 facilitates easier inspection and repair of connecting pipes, curtailing lengthy downtimes during maintenance cycles. This is particularly valuable in sectors where any halt in operations can lead to significant financial losses.
Moreover, flange 160s are designed with considerations for future scalability. Industries that anticipate scaling up operations need components that can adapt to expanding systems. Flange 160 offers a flexible solution that accommodates growth without necessitating a complete overhaul of existing infrastructure. This adaptability is a significant selling point, serving both current needs and future expansions.
Despite their robust features, flanges like the flange 160 must be properly installed and maintained to maximize their benefits. Proper installation techniques include ensuring perfect alignment and paying meticulous attention to torque specifications. Post-installation, regular inspections help in early detection of potential issues, allowing for preemptive maintenance and extending the lifespan of the flanges.
In conclusion, flange 160 presents a compelling choice for industries seeking reliability and efficiency in their piping systems. The combination of durable materials, proven performance records, and cost-saving benefits truly sets these flanges apart from their counterparts. Adopting flange 160 is not merely about keeping up with industry standards but about setting the benchmark for excellence in high-pressure applications. As innovation evolves, staying informed and integrating such cutting-edge solutions is vital for maintaining a competitive edge in the dynamic industrial landscape.