Flanges, integral components in various industries, often go unnoticed despite their pivotal role in the construction and manufacturing sectors. The myriad types of flanges, each designed for specific applications, underscore the complexity and precision required in their fabrication and selection. This exploration digs into the diverse world of flanges, providing insights gleaned from decades of industry experience and expertise.
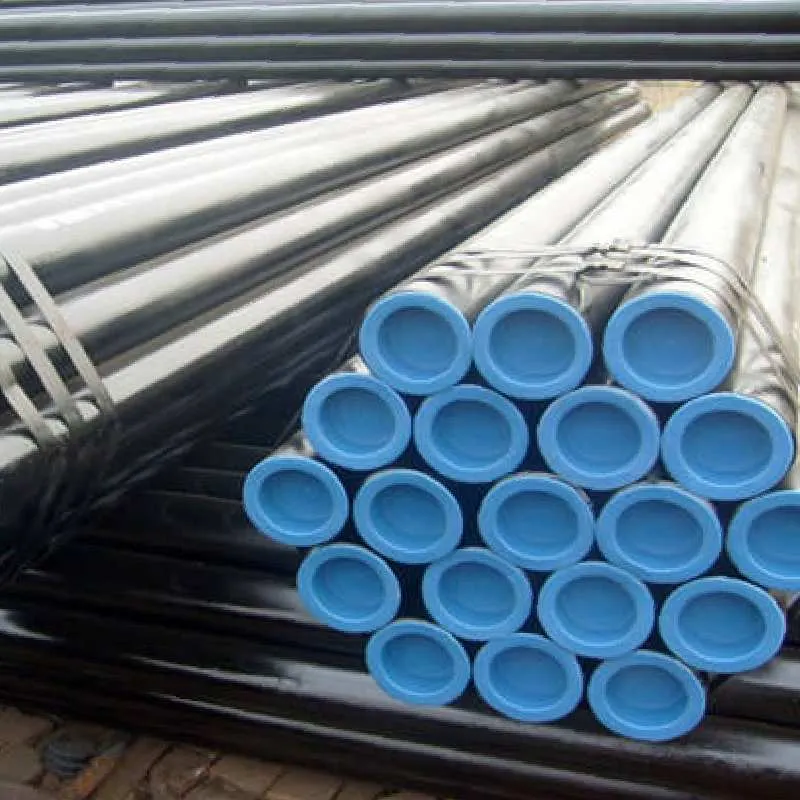
Flanges serve primarily as a means of connecting pipes, valves, pumps, and other equipment to form a piping system. They offer easy access for cleaning, inspection, and modification, underpinning their widespread use in industries ranging from oil and gas to chemical manufacturing and power generation. The reliability and durability of flanges make them indispensable in maintaining the integrity and functionality of piping systems.
Types of Flanges A Comprehensive Overview
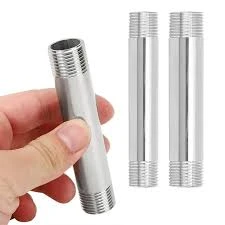
Understanding the different types of flanges is crucial for selecting the right component for a given application, ensuring both performance and safety. The most common types include
1. Weld Neck Flanges Recognized by their long, tapered hub, weld neck flanges are ideal for high-pressure applications. They are welded into the piping system, providing excellent stress distribution and reducing the risk of corrosion. The robust nature of weld neck flanges makes them suitable for extreme conditions, such as varying temperatures and pressures encountered in oil and gas pipelines.
2. Slip-On Flanges Easier to align than weld neck flanges, slip-on flanges slide over the pipe and are welded both inside and outside. This makes installation relatively straightforward. They are ideal for lower-pressure applications where quick and cost-effective installation is a priority.
3.
Socket Weld Flanges These are typically used for small high-pressure pipes. The pipe is fillet welded to the flange hub, which ensures a smooth bore and good flow characteristics within the pipe. Socket weld flanges are particularly prevalent in chemical environments where high leakage prevention is necessary.
4. Blind Flanges Serving as a cap for a piping system, blind flanges are used to block off a section of pipe or a nozzle on a vessel. They are essential for maintenance and safety, preventing flow and allowing pressure testing of the system. Their versatility and efficacy in sealing off conduits are crucial in safeguarding against potential leaks and bursts.
flanges and its types
5. Lap Joint Flanges Used in conjunction with a stub end, lap joint flanges are advantageous when frequent disassembly is anticipated. While they are not as robust in terms of pressure resistance as other types, their easy assembly and alignment make them popular in systems requiring regular inspection or cleaning.
6. Threaded Flanges Also known as screwed flanges, these are used for special applications where welding is not feasible. They are suitable for high-pressure applications, although they are predominantly used on small diameter, low-pressure systems. Their adaptability to various threading standards is an asset in flexible system design.
7. Ring Type Joint (RTJ) Flanges Designed for high-pressure and high-temperature applications, RTJ flanges feature a groove that holds a metal ring. As the flange bolts are tightened, the ring is compressed, creating a highly secure seal ideal for critical environments in the petrochemical and drilling industries.
Real World Applications and Considerations
The selection of flange types is influenced by factors such as the material of construction, compatibility with the fluid being transported, temperature and pressure conditions, and the overall cost-effectiveness of the installation. Materials such as stainless steel, alloy steel, and carbon steel are commonly used, each providing distinct advantages in terms of corrosion resistance, strength, and longevity.
Furthermore, the expertise of installers plays a significant role in the effectiveness of flange installations. Proper alignment and tightening ensure optimal performance, minimizing the risk of leaks and system failures. Regular maintenance and inspections are imperative for industries relying heavily on piping systems, as they prevent potential hazards and prolong service life.
In conclusion, flanges are versatile components that bring stability and efficiency to industrial systems. Their various forms cater to a wide array of applications, underscoring the importance of informed selection and competent installation. As industries continue to evolve and demand more robust and specialized solutions, the role of flanges will undoubtedly expand, cementing their status as foundational elements in modern engineering.