Flanges are a vital element in the realm of piping systems, serving as essential connectors that facilitate the assembly of pipelines, valves, pumps, and other equipment to create a secure, leak-proof, and efficient construction. Their versatile nature allows them to be utilized across various industries, including petrochemical, oil and gas, power generation, and water treatment, to name a few. Delving into the world of flanges, one quickly realizes the diversity in their types, each designed to meet specific requirements and applications.
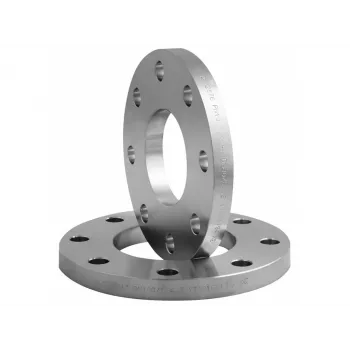
The most commonly used flange is the Weld Neck Flange. Distinguished by a long, tapered hub that transitions gracefully into the thickness of the pipe or fitting, the weld neck flange minimizes stress concentration, making it ideal for high pressure and severe temperature applications. Its design significance comes from the fact that the flange is welded directly to the pipe, effectively becoming part of the pipe, which provides smooth flow and minimal turbulence in high-pressure environments.
A Slip-On Flange is another popular choice, known for its simplicity and ease of installation. Unlike its counterparts, it slides over the pipe and is welded both inside and out to secure it in place. Its nature makes it cost-effective for both low-pressure services and less demanding applications. The preference for slip-on flanges is often due to their reduced installation effort, particularly in replacing or extending existing pipelines.
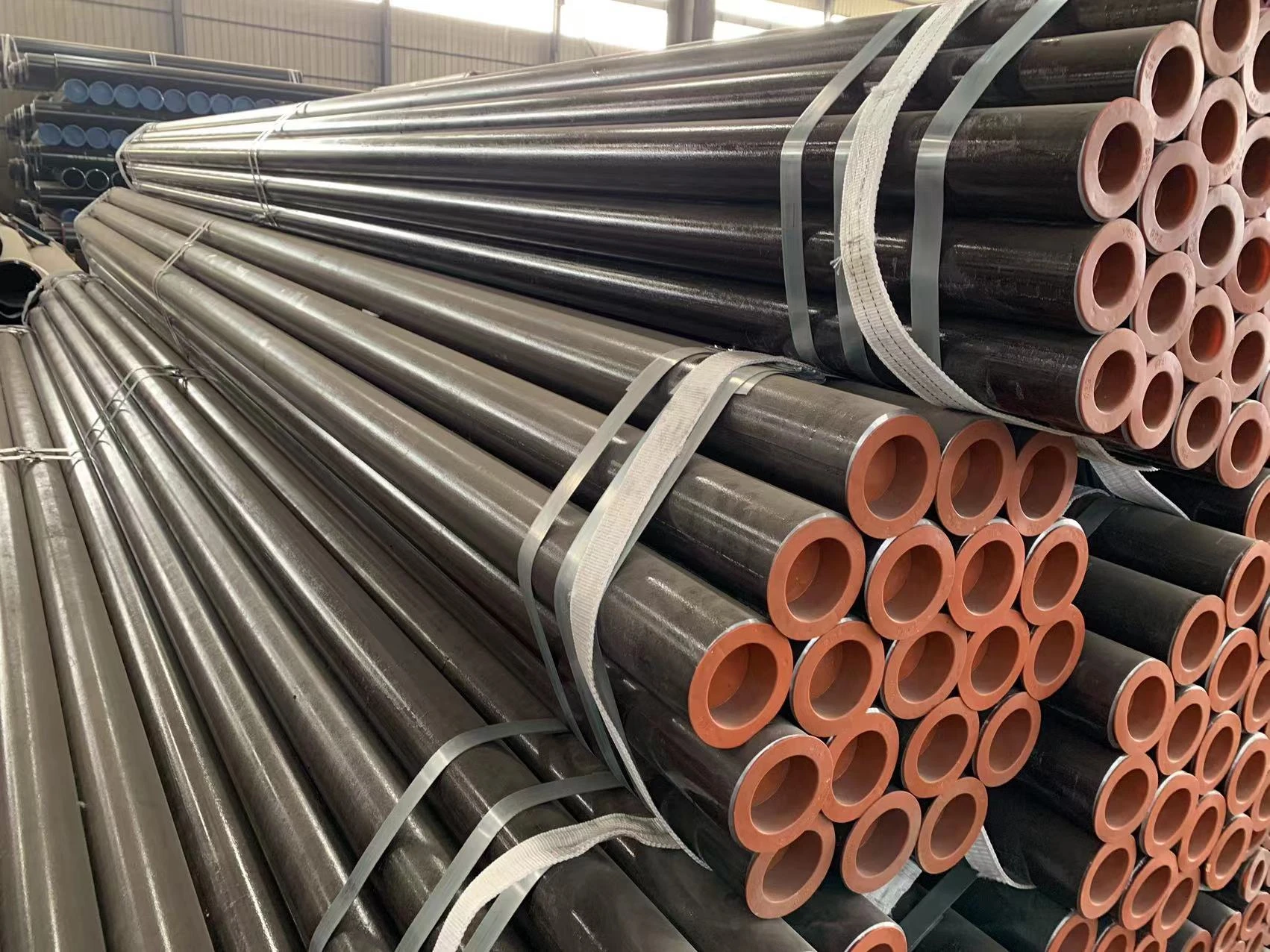
Blind Flanges represent the simplest form of flanges, primarily used for terminating the end of a piping system or vessel opening. With no bore, they provide easy access for cleaning, inspection, and modification of piping systems. Used extensively in petrochemical plants and shipbuilding, Blind Flanges can withstand higher pressures compared to other flanges because they are subject to internal pressure and their construction supports system stresses.
Socket Weld Flanges are characterized by the socket where the pipe is inserted before welding. This configuration is especially suitable for smaller sizes and allows for a clean, smooth bore, ensuring good flow characteristics. Often utilized in high-pressure systems where filler metals could lead to the weld being weaker than the pipe metal, socket weld flanges provide a strong and durable joint.
flanges types and pictures
Lap Joint Flanges differ significantly from their peers, as these require the use of a stub end. This two-piece assembly eliminates alignment issues, making them suitable for systems requiring frequent assembly and disassembly. The lap joint flange moves freely around the stub end, allowing for easy bolt alignment, while the actual sealing occurs between the stub end and the gasket. This makes them especially useful in systems subject to vibrations or thermal expansions.
Threaded Flanges offer a unique non-welded option, ideal for high-pressure applications where welding can present hazards. These are designed for pipes with external threads and are perfect for scenarios that require quick and easy connections without the need for welding.
Finally, the specialty of Orifice Flanges makes them distinctive as they accommodate orifice plates for flow metering, often utilized in instrumentation systems. These flanges have radial tapping for pressure gauges and other metering devices, making them critically important in accurate flow rate calculations.
In selecting the right flange, materials play a decisive role. Typically, flanges are crafted from robust materials such as stainless steel, carbon steel, and various alloy steels, adapting to specific environmental and operational demands. Appropriate material selection ensures long-term resilience, resistance to corrosion, and durability under varying temperature and pressure conditions.
In conclusion, understanding the types of flanges and their respective applications is key for engineers, fabricators, and procurement officers to ensure the integrity and efficiency of piping systems. Recognition of their individual roles not only leads to optimized system performance but also assures safety, reliability, and efficiency, thus maintaining the pipeline's operational success across various industries. Through comprehensive expertise, knowledge sharing, and continuous advancements, flanges remain an indispensable component in modern engineering solutions.