Flange taps play an essential role in a wide array of industrial applications, serving as a critical component in the measurement of fluid flow within pipes. Their precision and reliability make them indispensable in sectors such as petrochemicals, water treatment, and manufacturing. However, understanding their practical applications and advantages requires a deep dive into their construction, functionality, and installation process.
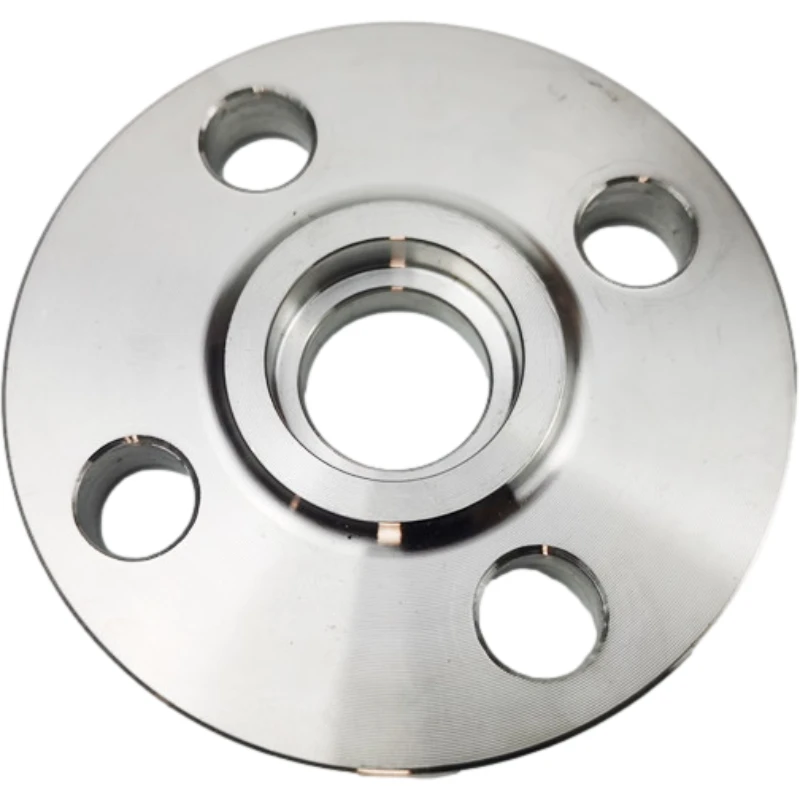
Flange taps are typically located one inch from the pipe wall and serve as points for pressure measurement in differential pressure flow meters, such as orifice plates. This placement is crucial as it ensures accurate readings by eliminating the interference of flow disturbances that might skew the data. Unlike other pressure taps, flange taps provide greater ease of maintenance and replacement, as they can be directly integrated into the flange—a mechanical device providing a robust connection between the pipe sections.
The expertise in using flange taps comes from their precise engineering. Typically manufactured from stainless steel or carbon steel, their durability under extreme conditions—high pressure, temperature variations, and corrosive environments—demonstrates their reliability. A knowledgeable engineer understands that selecting the correct material and type of flange tap is vital for ensuring operational efficiency and longevity, which can prevent costly downtime and emergency repairs.
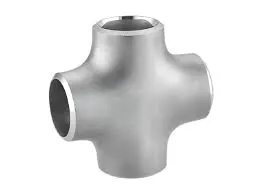
Authoritativeness in the field of flange taps is demonstrated through a comprehensive understanding of standards and regulatory compliances. Organizations such as the American Petroleum Institute (API) and the International Organization for Standardization (ISO) set guidelines that must be adhered to, ensuring that flange taps meet safety and performance benchmarks. This adherence not only guarantees product reliability but also instills confidence among stakeholders regarding the quality of the measurement systems employed in their operations.
flange taps
Trustworthiness is further established through rigorous testing and proven performance in real-world applications. Flange taps undergo substantial testing phases, including flow calibration and pressure testing, to ensure they operate flawlessly under specified conditions. These tests validate the accuracy of the flange taps, which is imperative for process control and optimization in industrial systems.
Experience in deploying flange taps effectively involves understanding the nuances of their installation and integration into existing systems. It is essential to consider factors such as the orientation of the tap, the type of fluid, and the operational environment. Professionals in this field leverage their experience to optimize the positioning and installation, minimizing potential points of failure or measurement inaccuracies.
Product selection should also involve consideration of technological advancements, such as smart taps equipped with sensors that enable real-time monitoring and data analytics. These innovations enhance the capability of standard flange taps by providing actionable insights that can lead to process improvements and predictive maintenance strategies, ultimately saving costs and resources in industrial operations.
In conclusion, flange taps offer more than a simple solution for flow measurement; they incorporate sophisticated design, strict adherence to industry standards, and are backed by empirical data and real-world applications. They are an archetype of how traditional mechanical components are evolving through material science and digital technology integration, providing precise, reliable, and efficient performance crucial for optimal industrial operations. For industries seeking accurate flow measurement and control, investing in high-quality flange taps, complemented by expert installation and maintenance, is a decision that pays dividends in reliability and efficiency over the operational lifespan.