In the world of industrial piping systems, pipe flanges play a crucial role in maintaining the integrity and functionality of the assembly. As an essential component, flanges are the backbone of many mechanical networks, ensuring that pipes are adequately connected without leaks. Understanding the different types of pipe flanges, their applications, and their advantages is critical for anyone involved in designing, maintaining, or operating piping systems.
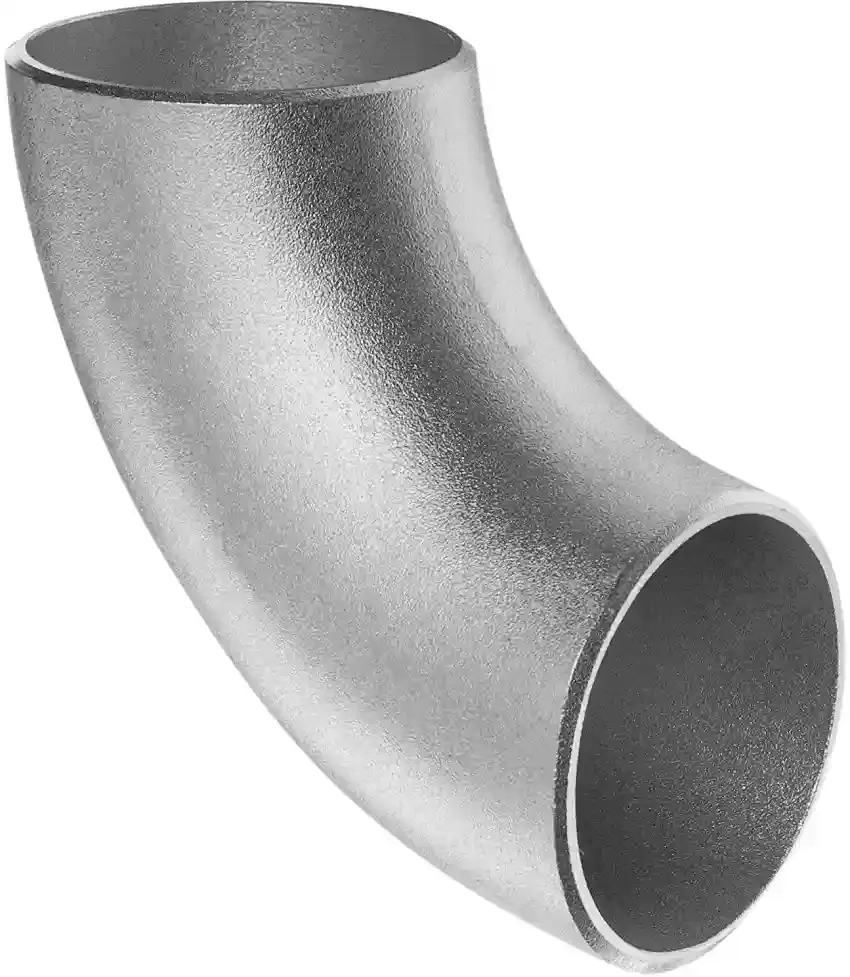
One primary type is the Weld Neck Flange, which is highly preferred in high-pressure environments. Its distinctive feature, a long tapered hub, reinforces the flange and the welded joint, minimizing the stress concentration at the base. Engineers trust weld neck flanges for their ability to handle extreme temperature fluctuations and high-pressure applications, making them ideal for chemical plants and gas pipelines. The secure, welded connection ensures minimal leakage and improved durability, underscoring its reliability.
Slip-On Flanges offer another alternative, particularly favored for their cost-effectiveness and ease of installation.
Unlike weld neck flanges, they slide over the pipe and are then fillet welded in place. This design facilitates quicker assembly, saving both time and labor. While not suited for high-pressure scenarios, slip-on flanges are perfect for low-pressure applications where cost efficiency and simplicity are prioritized, such as in water treatment systems and less demanding pipeline projects.
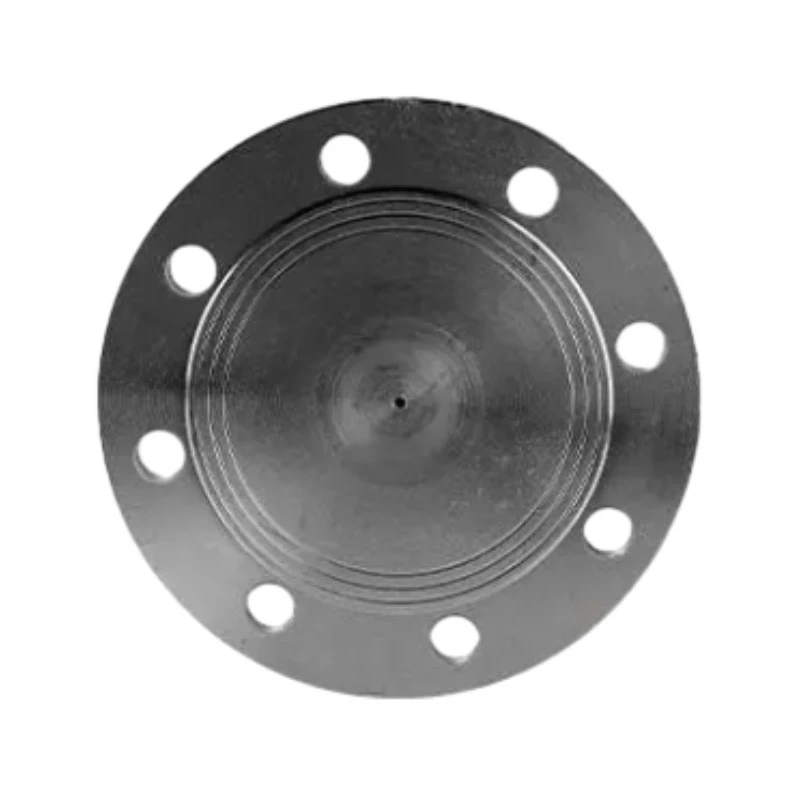
Socket Weld Flanges, characterized by their socket-like design that supports the insertion of the pipe before welding, are ideal for small diameter and high-pressure pipes. These flanges provide excellent fatigue resistance in cyclic load settings due to their monolithic design that distributes stress evenly across the flange and pipe. This makes them particularly useful in chemical processing industries where steady, high-pressure operations are commonplace.
pipe flange types
The Lap Joint Flange is another notable type designed for applications requiring frequent dismantling. It is typically used with a stub-end, facilitating quick assembly and disassembly, which is particularly beneficial in maintenance-intensive environments like food processing plants. Though the pressure ratings are not as robust as other flanges, their ease of use and ability to accommodate misalignments make them indispensable in systems where cleaning and inspection are routine.
Blind Flanges serve a unique yet critical role, effectively sealing off the ends of piping systems. Engineers employ blind flanges both to terminate piping and to allow for future system expansions or modifications. Their ability to withstand pressure from internal pipe flow without passage closure is invaluable in testing pipeline equipment and temperature flow settings, proving indispensable in petrochemical and high-pressure fluid systems.
Last but not least, Threaded Flanges are used primarily in scenarios where welding is inadvisable. Their design allows pipes to be screwed into the flange, making installation straightforward. This particular flange type is often employed in small diameter, high-pressure applications in environments with explosive hazards, providing a reliable seal without needing a welded joint.
Navigating the diverse types of pipe flanges demands a comprehensive understanding of their unique applications and limitations. Professionals must consider factors like pressure capacity, temperature resilience, installation ease, and maintenance requirements when selecting the appropriate flange type. By leveraging expertise and authoritative knowledge in this field, industries can optimize their piping systems for safety, efficiency, and longevity, ensuring the seamless transmission of fluids and gases crucial to their operations.