Gaskets play an essential role in preventing leaks at the flange connection in various applications across multiple industries. These seemingly simple components demand careful consideration, given the wide range of materials and designs available. A clear understanding of the types of gaskets for flanges is essential for selecting the right solution, ensuring system efficiency, safety, and longevity.
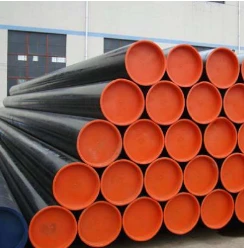
Spiral Wound Gaskets stand out due to their versatility and reliability. They comprise a mix of metallic and non-metallic materials, affording them resilience under high pressures and temperatures. These gaskets are constructed using a metallic strip and a non-metallic filler wound together in a series of concentric spirals. The result is a gasket that excels in handling fluctuating temperature and pressure conditions, making it suitable for applications in oil and gas refineries, chemical plants, and power generation industries.
Sheet Gaskets, typically fashioned from materials such as graphite, rubber, or PTFE, are known for their adaptability and affordability. These gaskets are often used in less demanding environments, providing a reliable seal in a broad range of applications. Graphite sheet gaskets are praised for their thermal resistance, whereas PTFE gaskets offer excellent chemical inertness. Thus, selecting the correct material is crucial for matching specific operational environments.
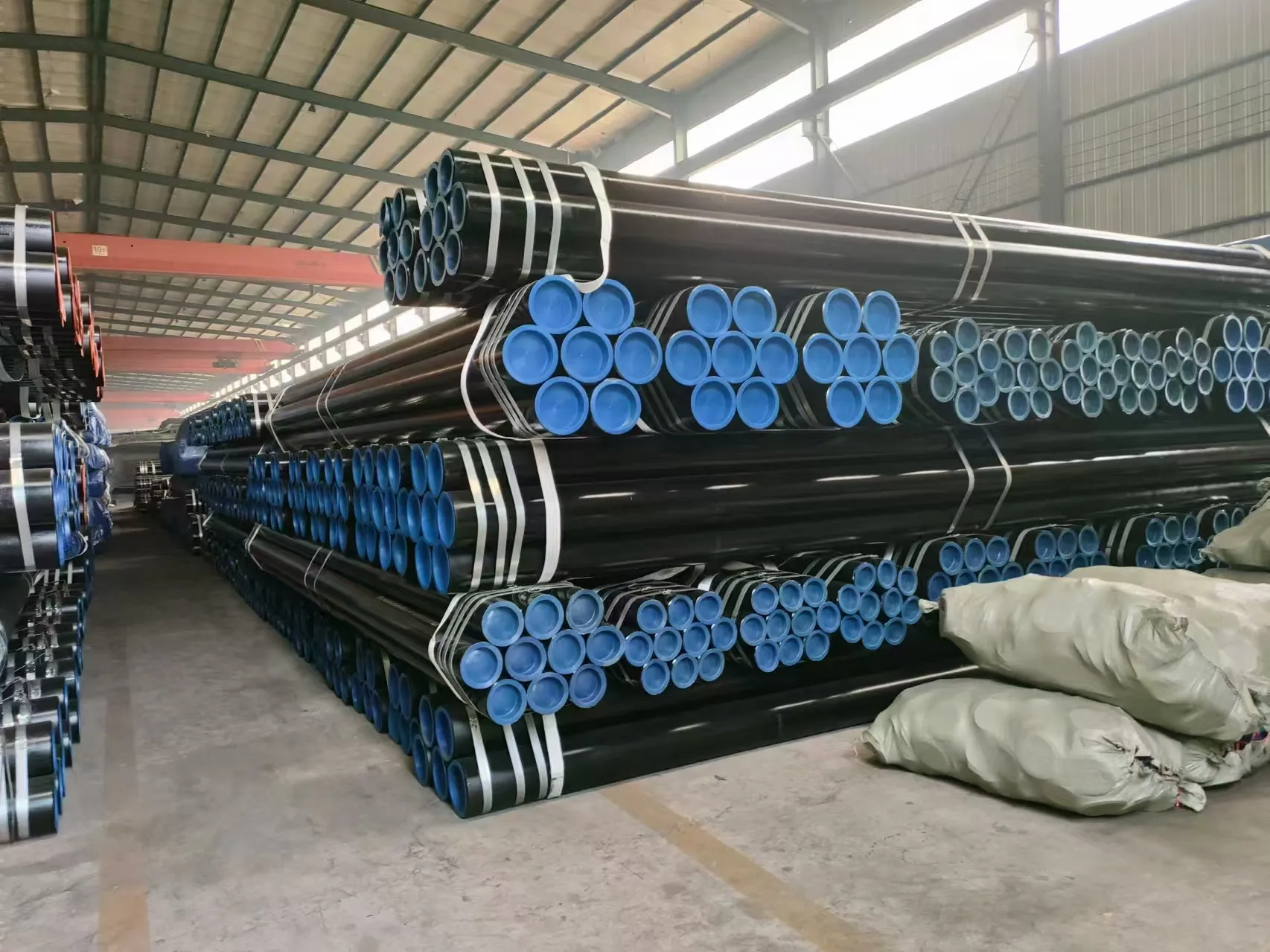
Ring Type Joint (RTJ) Gaskets are specially designed for high-pressure applications. Made from a metal ring, these gaskets are utilized in the oil and gas industry to prevent leaks in pipe connections. The hardness of the material is slightly less than that of the flanges, which allows the gasket to deform and create a tight seal when bolted. RTJ gaskets require precise machining of the flange faces to ensure proper functionality, demanding expertise in their installation and maintenance.
Kammprofile Gaskets provide a balance between flexibility and strength. These gaskets have a corrugated metal core with a soft sealing layer, which creates a tight seal with minimal torque. They are often used when dealing with harsh chemical environments, as the inner metal core provides robustness, while the outer layers offer a degree of conformability. Kammprofile gaskets are praised for their ability to resist blowout and maintain a reliable seal under varying loads, making them an excellent choice for complex sealing scenarios.
types of gaskets for flanges
For environments where hygiene is paramount, as in the food and pharmaceutical industries, Gasket Tape offers a compelling solution. It is especially advantageous in systems where quick assembly and disassembly are frequent. This tape is commonly constructed from PTFE or expanded PTFE, providing a clean, non-contaminating surface that meets strict industry standards. The ease of application and removal makes gasket tape an attractive option for operations that incur frequent maintenance or cleaning.
Corrugated Metal Gaskets combine strength with resilience. They are crafted with a thin metal core and covered with a soft facing material. These gaskets are effective across a variety of applications, particularly where uneven flange surfaces might pose a challenge. The core of these gaskets offers structural integrity, while the soft facings provide excellent sealing characteristics. Their adaptable nature means they are often found in chemical processing plants and piping systems that undergo regular fluctuations in stress.
In selecting a gasket, consider factors such as the nature of the fluid being sealed, the operating temperature and pressure, the material of the pipe and flange, and compliance with industry standards. Consulting with a gasket manufacturer or an experienced engineer will ensure the most authoritative advice, thereby establishing trust in the decision-making process.
Expertise in gasket selection not only impacts operational efficiency but also ensures compliance with safety standards and prolongs the lifespan of system components. A well-chosen gasket leads to reliable sealing solutions, minimal maintenance costs, and ultimately a lower total cost of ownership. Understanding these diverse types of gaskets for flanges equips professionals with the knowledge to address varied sealing demands, fostering a safer and more efficient operational environment.