Flanges play a crucial role in various industrial applications, particularly in piping systems. With stainless steel (SS) flanges, industries ensure a robust connection that can withstand high pressures and temperatures. Their durability and resistance to corrosion make SS flanges an ideal choice for several sectors, including oil and gas, petrochemicals, and water treatment. In this article, we will explore the different types of SS flanges, offering insights from both an expertise-laden and real-world experience perspective.
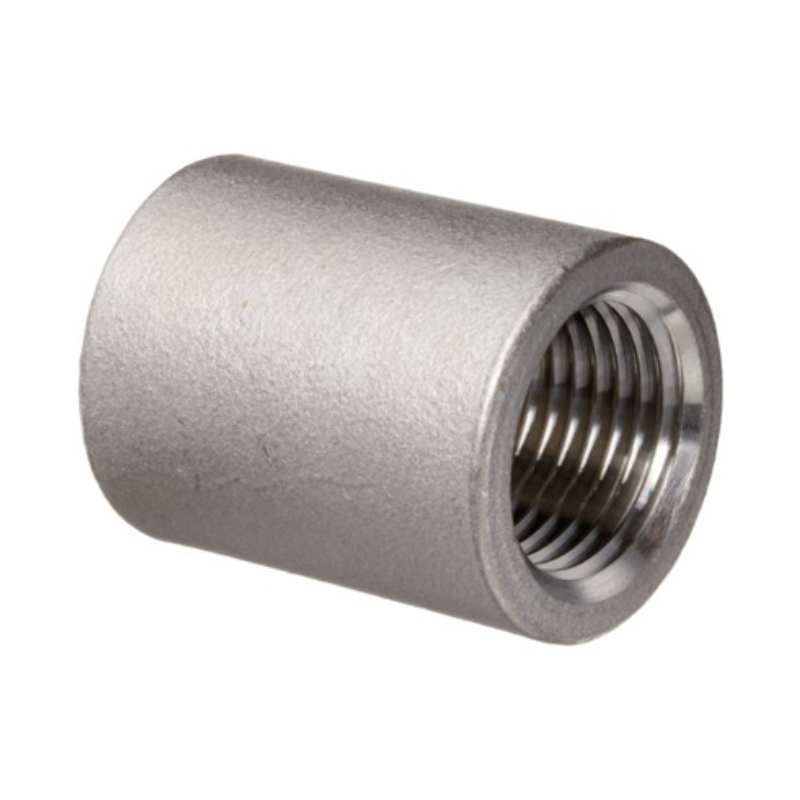
Slip-On Flanges
Slip-on flanges are popular because of their ease of installation.
As the name suggests, these flanges slip over the pipe and are then welded in place. This type ensures alignment between pipes, making it an excellent choice for systems that require regular maintenance or replacements. Industries prefer slip-on flanges for their lower material costs and simplistic welding requirements. However, they may not be the best choice for high-pressure applications due to their relative mechanical strength.
Weld Neck Flanges
For high-pressure environments, weld neck flanges are the go-to option. Recognizable by their long tapered hub that gradually transitions to the pipe, they provide excellent strength and resilience, reducing stress concentration and enhancing fluid flow. The neck is butt-welded to the pipe, ensuring a strong and reliable joint. This type is particularly suited for critical applications where thermal and mechanical stresses are factors. Through years of practical application, experts have noted the reliability that weld neck flanges bring in maintaining system integrity under extreme conditions.
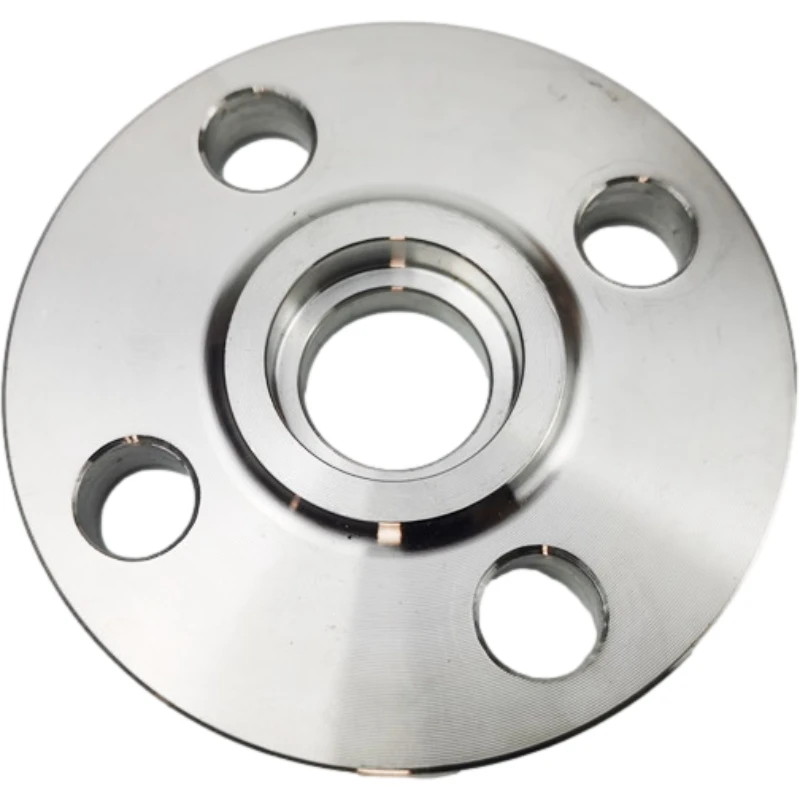
Blind Flanges
Often used to terminate sections of a piping network, blind flanges are unique because they don’t have a bore. This feature means they are instrumental in providing a positive closure to the end of pipes, valves, or pressure vessel openings. In maintenance and testing phases, blind flanges become invaluable, allowing for easy access with no leakage. The material integrity of SS makes them resistant to environmental and chemical erosion, enhancing their application across various industries that deal with toxic substances.
Socket Weld Flanges
Socket weld flanges find their place in smaller pipe networks requiring high structural integrity. In these flanges, pipes are inserted into a socket at the end of the flange and then welded, offering a smooth bore and better fluid flow in the process. This type of flange is particularly favorable in applications where avoiding leakage paths is critical, and they are typically preferred in systems with lower pressure and temperature settings.
ss flange types
Lap Joint Flanges
A unique feature of lap joint flanges is their use in conjunction with a stub end. The flange itself doesn’t come into contact with the fluid as the stub end is placed between the pipe and the flange, which allows for rotation to align holes easily. They are beneficial in systems where frequent dismantling is required for inspection and maintenance. Their ease of assembly disassembly is a favored feature in industries where corrosion-resistance through material separation is key.
Threaded Flanges
Also known as screwed flanges, these are a great solution for specific situations where welding is not feasible. In environments with highly explosive materials, where welding could risk safety, threaded flanges are employed. They offer an advantage in scenarios requiring easy installation or removal and work well under both high and moderate pressure systems. However, due to the nature of the connection, they might not be as robust as welded counterparts.
Flange Faces and Finishes
Beyond material and type, the face type and finish of a flange affect its compatibility with gaskets and sealing performance. SS flanges typically come with types like raised faces or flat faces, each offering distinct sealing advantages. When selecting a flange, it's vital to ensure that the face type aligns with the gasket and bolting options to maximize leak-proof performance.
Concluding Thoughts
Picking the right type of SS flange extends beyond their categorization. Factors like environment, pressure, temperature, and application frequency are integral considerations. As industries continue to innovate and adapt, SS flanges must meet ever-evolving standards for safety, durability, and efficiency. By focusing on these criteria, expert engineers can optimize both safety and performance across complex piping systems.