Welded steel pipes have become a cornerstone in a plethora of industries, from construction to energy, owing to their robustness and versatility. This article delves into the comprehensive world of welded steel pipes, addressing their manufacturing process, applications, and the factors that make them a favored choice in various industrial sectors, emphasizing experience, expertise, authoritativeness, and trustworthiness.
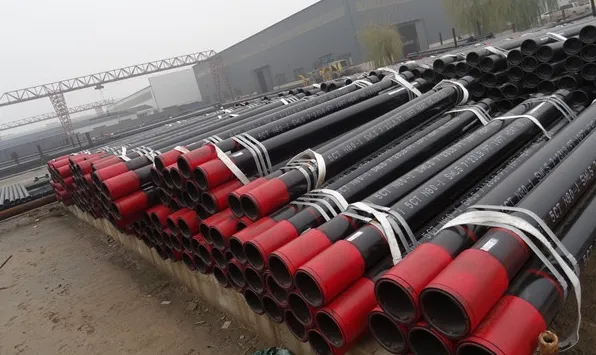
The journey of a welded steel pipe begins with selecting the appropriate material. High-quality steel is chosen for its strength and ability to withstand extreme conditions. The steel is then rolled into a tube and welded using advanced techniques such as Electric Resistance Welding (ERW) or Spiral Submerged Arc Welding (SSAW), depending on the intended application. This welding process is critical,
as it determines the integrity and durability of the pipe. The seamless appearance and consistent wall thickness of welded pipes enhance their strength, making them ideal for high-pressure environments.
In terms of applications, welded steel pipes are ubiquitous. They are prominently used in the construction industry for structural support and in the oil and gas sector for transporting liquids and gases due to their ability to maintain integrity under pressure. Additionally, they are essential in water supply systems, sewage transport, and in the automotive industry for exhaust systems. Each application demands different specifications, and manufacturers must adhere strictly to industry standards to ensure safety and reliability, underscoring trustworthiness and authority in the field.
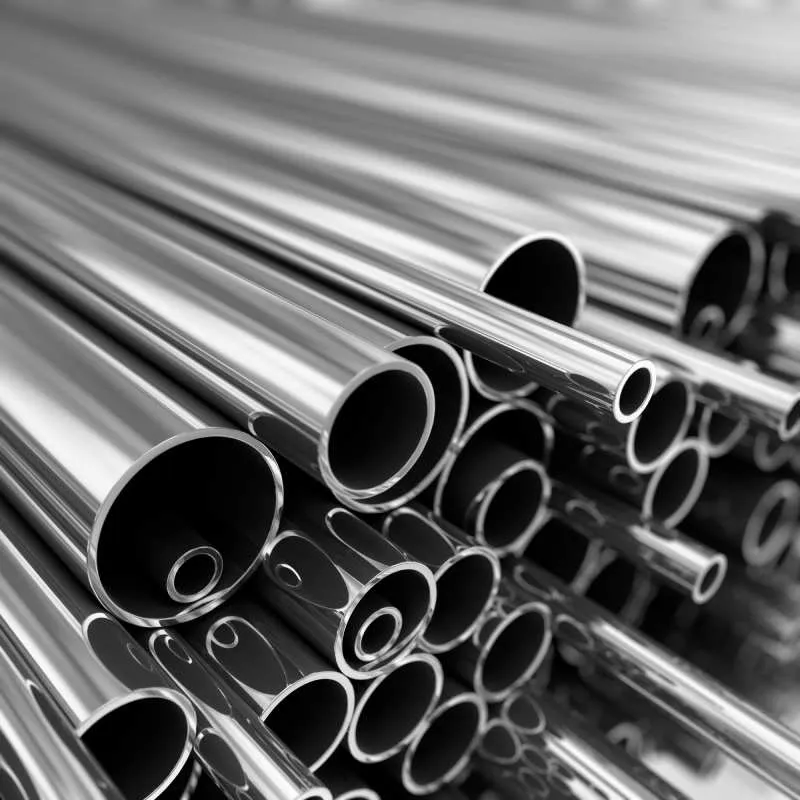
Real-world experiences amplify the reliability and expertise associated with welded steel pipes. For instance, in oil refineries, where conditions are extreme and the risk of corrosion is high, welded steel pipes have been proven to last longer with minimal maintenance, thus providing cost-effective solutions. Similarly, their use in urban infrastructure projects has demonstrated their capability to withstand seismic activities without compromising performance, solidifying their status as a reliable choice in essential services.
welded steel pipe
The expertise involved in producing welded steel pipes is not to be understated. Professionals in this field undergo extensive training and stay abreast of technological advancements to ensure the highest standards are met. The diversity in welding techniques allows for customization in pipe production, meeting specific industry requirements. This level of expertise ensures that welded steel pipes are not only functional but also efficient, fulfilling unique needs across different sectors.
Authoritativeness in the welded steel pipe industry is maintained through rigorous quality control and adherence to international standards like ASTM and ISO certifications. Manufacturers engage in consistent testing during and after production to ensure each pipe piece meets the required specifications. This commitment to quality not only enhances trustworthiness but also positions welded steel pipes as a definitive choice for industries prioritizing safety and durability.
Furthermore, sustainability has become a pivotal factor driving trust in welded steel pipes. Leading manufacturers incorporate eco-friendly practices by using recyclable materials and implementing processes that reduce carbon footprints. This sustainable approach aligns with global environmental standards, appealing to industries conscious of their environmental impact while emphasizing the reliability and ethical responsibility of welded steel pipe production.
To conclude, welded steel pipes epitomize a blend of robust engineering, expert manufacturing, and enduring trust. Their role in critical industries is supported by comprehensive quality assurance, a commitment to sustainability, and a track record of real-world reliability. These elements not only reinforce their market authority but also ensure that welded steel pipes continue to be a preferred choice across various sectors, providing solutions that meet both current demands and future challenges with precision and integrity.