Different flange types play a pivotal role in industrial applications, each designed to meet unique requirements in piping and mechanical systems. Flanges serve as the backbone of pipeline networks, connecting shafts and facilitating the transfer of fluids across various types of equipment. Understanding the nuances of different flange types is essential to selecting the right product for your project and ensuring reliability and safety. This article explores the distinct types of flanges, their applications, and their benefits, offering insights grounded in industry expertise and experience.
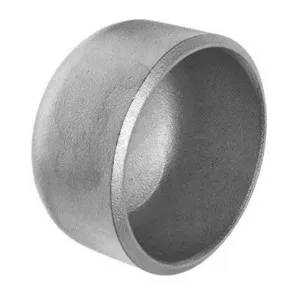
The most common flange types include weld neck flanges, slip-on flanges, socket weld flanges, lap joint flanges, threaded flanges, and blind flanges. Each type is crafted to cater to specific scenarios, characterized by their unique design features and compatibility with different environmental conditions.
Weld neck flanges are recognized for their long tapered hub which transitions the thickness from the flange base to the pipe or fitting. This design is particularly beneficial for high-pressure applications, offering excellent strength and integrity due to the full penetration welds used in their installation. Their usage in high-stress environments, such as oil and gas industry pipelines, is testament to their durability and reliability under extreme conditions.
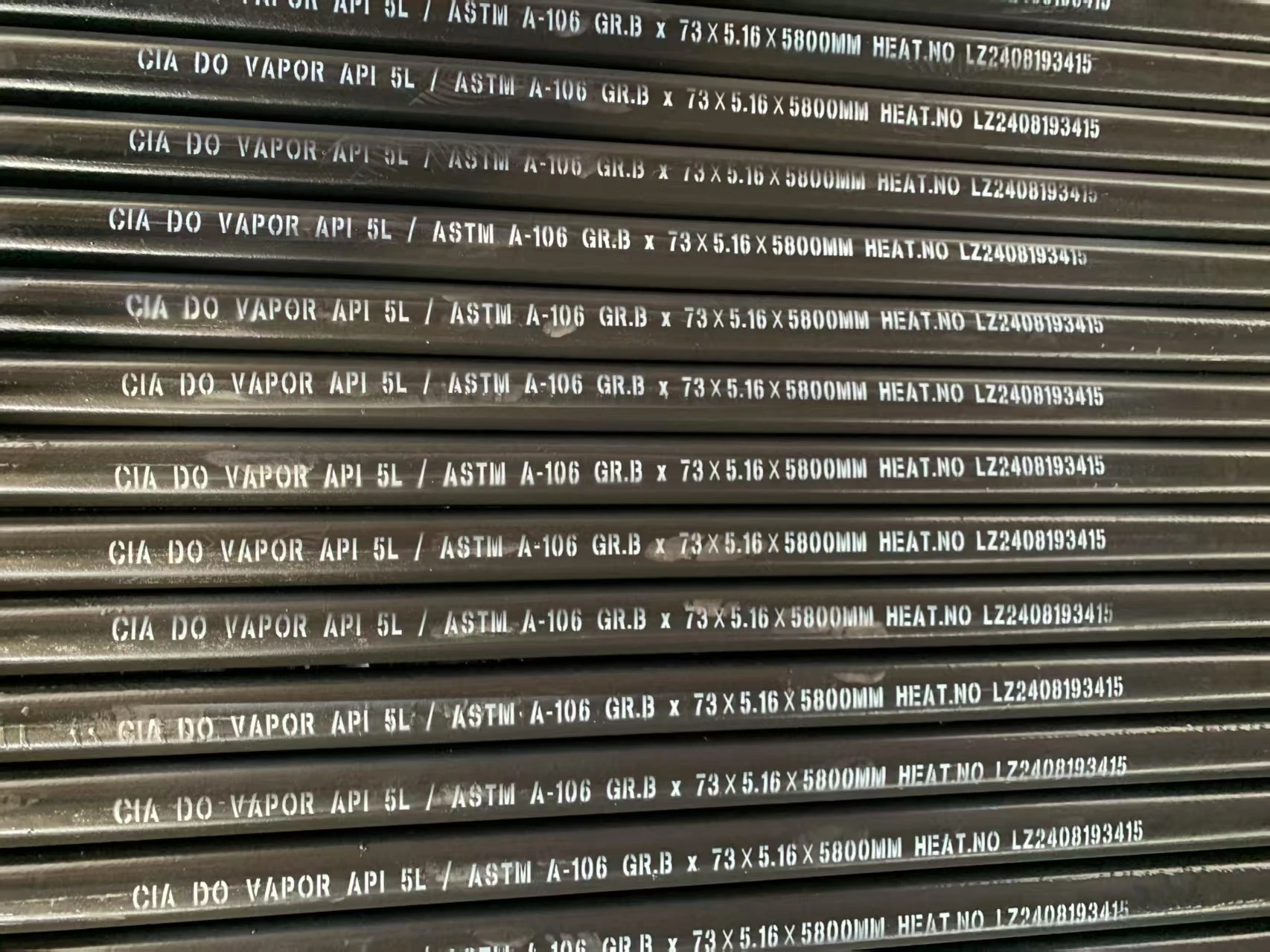
Slip-on flanges, on the other hand, offer ease of installation and alignment. They are often preferred where space constraints inhibit the use of more robust flanges. Although they are less durable than weld neck flanges under high-pressure situations, their cost-effectiveness and simplicity make them ideal for low-pressure and low-temperature settings. Their versatility is deployed in water treatment plants and other applications where frequent maintenance might be necessary.
Socket weld flanges are similar in purpose to slip-on flanges but have a recessed area where the pipe fits into. Designed predominately for small-diameter, high-pressure piping, these flanges are employed where strength integrity is important. The welding process used ensures a smooth bore and strong connection, reducing the likelihood of leakage. This makes them ideal for chemical processing or seawater systems.
Lap joint flanges differ from other types as they are typically used with a matching stub end. The flange simply slips over the stub end and rotates for easy alignment. While not inherently strong, they are suitable for systems requiring frequent inspection, cleaning, or dismantling. Used in industries where corrosive materials are a concern, such as in maritime environments, they allow for the use of high-cost material only on the stub end, reducing overall costs.
different flange types
Threaded flanges offer a unique advantage in systems where welding is not viable. Typical in low-pressure situations and smaller diameters, the flange is screwed onto a pipe using matching threads. This makes them easily removable and ideal for non-critical, low-temperature applications like utility power plants.
Blind flanges, serving as terminators or blockages in pipelines, are crucial in systems requiring isolation or future expansion. Often utilized during pressure testing, these flanges ensure that areas of the pipeline that need to be isolated do not get fluids or gases passing through. Their solid design handles high pressure well, offering a reliable seal.
In each of these flange types, material choice plays a vital role. Stainless steel, carbon steel, and alloys are commonly used, each selected for their specific environmental resistance and mechanical properties. Stainless steel offers excellent temperature and corrosion resistance, while carbon steel provides foundational strength at an economic cost. Selecting the right material based on environmental conditions, chemical compatibility, and temperature is a crucial step in flange selection.
Safety and efficiency are paramount in industrial processes, making the selection of appropriate flange types crucial. Understanding each type's specific application and benefits not only helps in making informed decisions but also in maintaining system integrity and operational longevity. Proper selection and installation can minimize downtime, enhance safety, and ensure regulatory compliance, particularly in sectors where standards are stringent.
As technology advances, flange designs continue to evolve, presenting new opportunities for improved performance and safety. Engineers and industry experts recommend a thorough assessment of operational requirements, anticipating both current and future demands to ensure that the flange systems are up to date and reliable.
Comprehensive understanding and application of different flange types demand more than just technical knowledge—they require a blend of field experience, expertise, and adherence to authoritative standards to establish trustworthiness and maintain industry standards. Properly managed, flanges contribute significantly to the efficient and safe operation of mechanical systems across diverse industries.