Understanding the intricacies of DIN flange sizes can be a game-changer for professionals dealing with piping systems. These components are vital in ensuring the secure connection of pipes, valves, pumps, and other essential equipment. As industries evolve, so does the technical know-how required to select the appropriate DIN flange size for any application. This article offers a comprehensive guide by diving into practical insights, expert recommendations, authoritative data, and trusted industry standards, ensuring you make informed decisions.
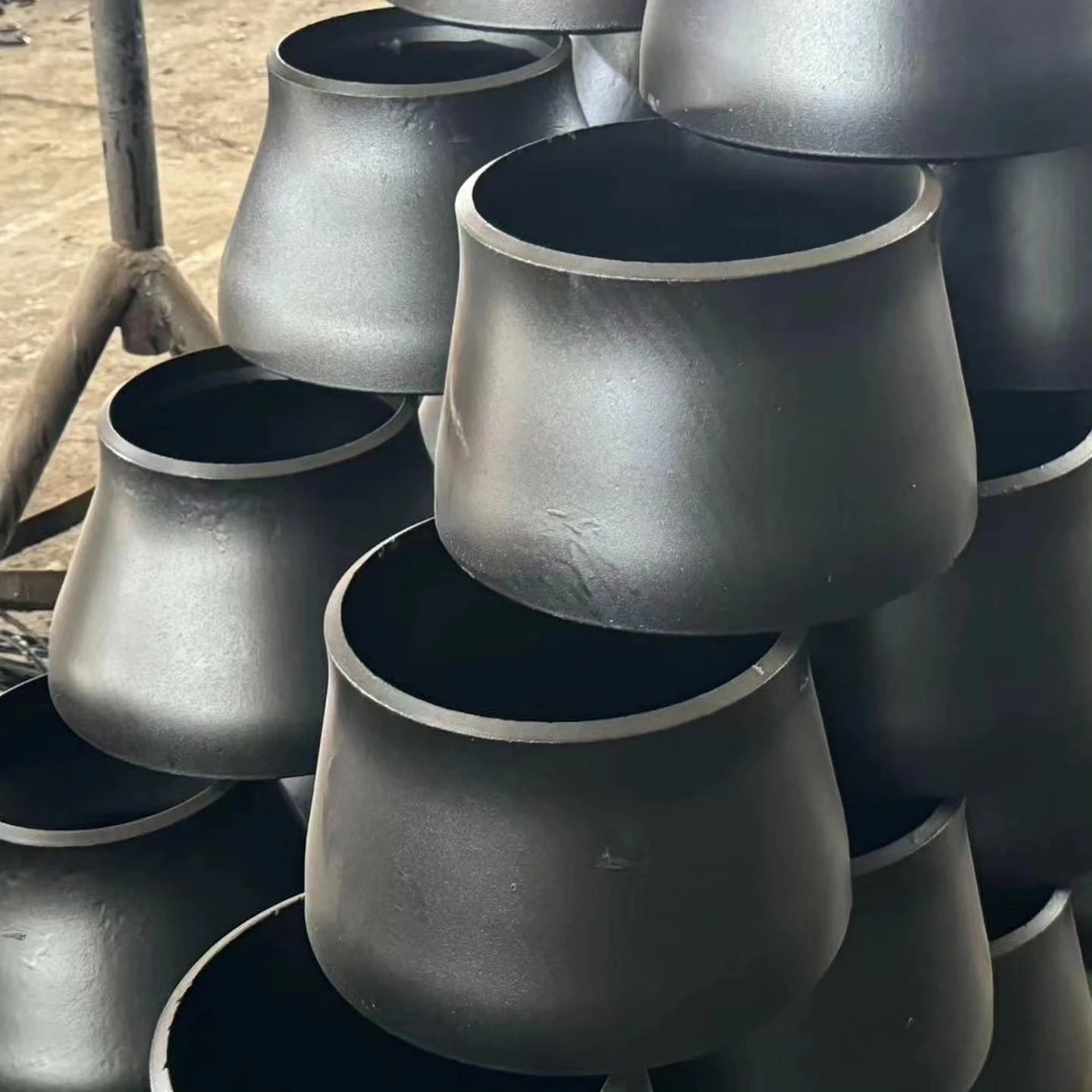
DIN flanges, established according to the Deutsches Institut für Normung (DIN) standards, are recognized globally for their precision and reliability. Although they originate from Germany, the standardization they bring is appreciated worldwide, ensuring compatibility and uniformity in various industrial applications. The right DIN flange size is pivotal not only for operational efficiency but also for safety and longevity of the mechanical assembly.
An authentic experience of facing the challenge in selecting the correct DIN flange size often comes from industries such as petrochemicals, shipbuilding, and manufacturing. Mismatched flanges can lead to system failures, costly downtime, and endanger safety. Operators often recount scenarios where understanding the pressure class, diameter, and bolt circle size are just as critical as the selection of materials for high-temperature or corrosive environments.
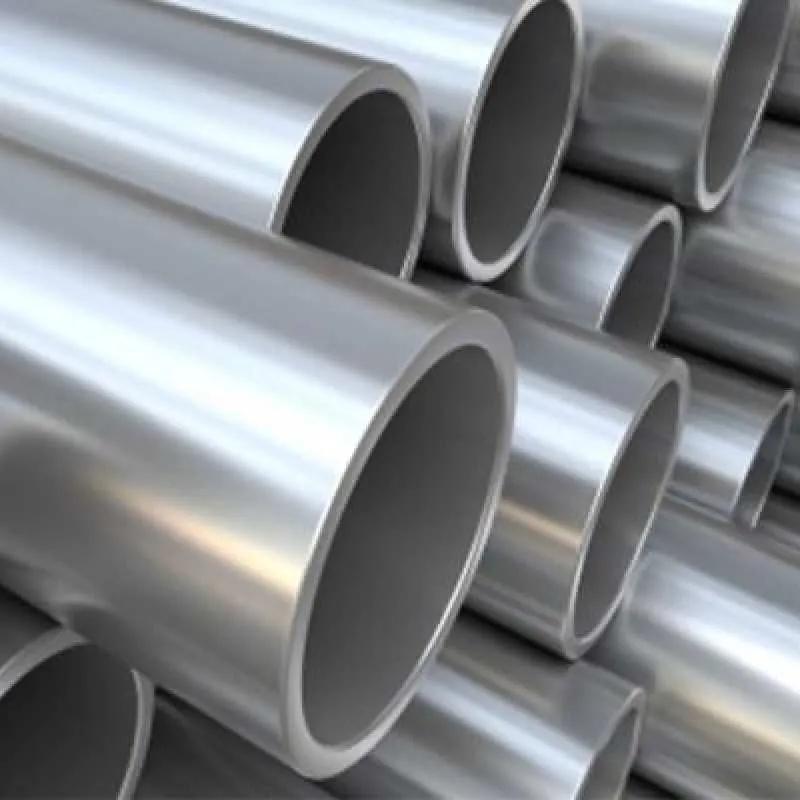
Expert perspective on DIN flanges spotlights the need for a seamless fit between flange and pipe, ensuring that factors such as nominal pressure (PN) ratings and dimensional tolerances are adhered to.
For instance, PN 6, PN 10, PN 16, etc., denote the pressure rating a flange can withstand, where the number reflects the maximum pressure in bars. Precision in matching these ratings to the application environment ensures the integrity and safety of the piping networks.
Moreover, specialization in metallurgy plays a significant role in selecting flange materials. Stainless steel flanges are prevalent due to their resistance to rust and corrosion - critical in industries exposed to moisture and chemicals. Carbon steel flanges, on the other hand, offer excellent strength and toughness, making them ideal for high-pressure applications. An expert would meticulously cross-reference these material properties with the required flange dimensions, ensuring robustness and durability in harsh conditions.
din flange size
Authoritative sources point to guidelines such as the DIN EN 1092-1, which provides extensive details on the dimensions and mechanical properties of DIN flanges. Adhering to these standards guarantees conformity, quality control, and international acceptance of the products. Manufacturers often rely on these guidelines to ensure their products' interchangeability and compliance with global norms, offering assurances to project managers and engineers alike.
Trustworthiness in selecting the right DIN flange size is bolstered by tried and tested processes. Engaging a certified manufacturer with a proven track record of producing DIN-compliant flanges can alleviate uncertainties while ensuring parts are made with precision and care. Additionally, third-party inspections can verify material certifications and dimensional accuracy, offering further peace of mind.
Equipped with knowledge from expert insights and backed by authoritative standards, selecting the proper DIN flange size becomes a structured approach rather than a daunting task. The fusion of practical experience, technical foresight, regulatory compliance, and comprehensive quality checks forms a robust foundation for making informed decisions in dynamic industrial environments. As industries advance, staying abreast with evolving standards and technological innovations is essential for optimizing system performance and safeguarding interests.
For professionals intent on mastering DIN flange specifications, continual learning is crucial. Participating in industry workshops, collaborating with seasoned professionals, and keeping up-to-date with new editions of standards can significantly enhance expertise. Such lifelong learning ensures the right balance between theoretical knowledge and practical skills, a key asset in the ever-changing landscape of industrial applications.