Flange valves have become an integral component in numerous industrial applications, adored for their durable construction and reliability in regulating fluid flow. Professionals seeking optimized and efficient systems often turn to flanged valves due to their flexibility in high-pressure environments. This piece explores the practical utility and technical specifications of flange valves, offering insights drawn from extensive industry experience, expert advice, authoritative resources, and reputable practices.
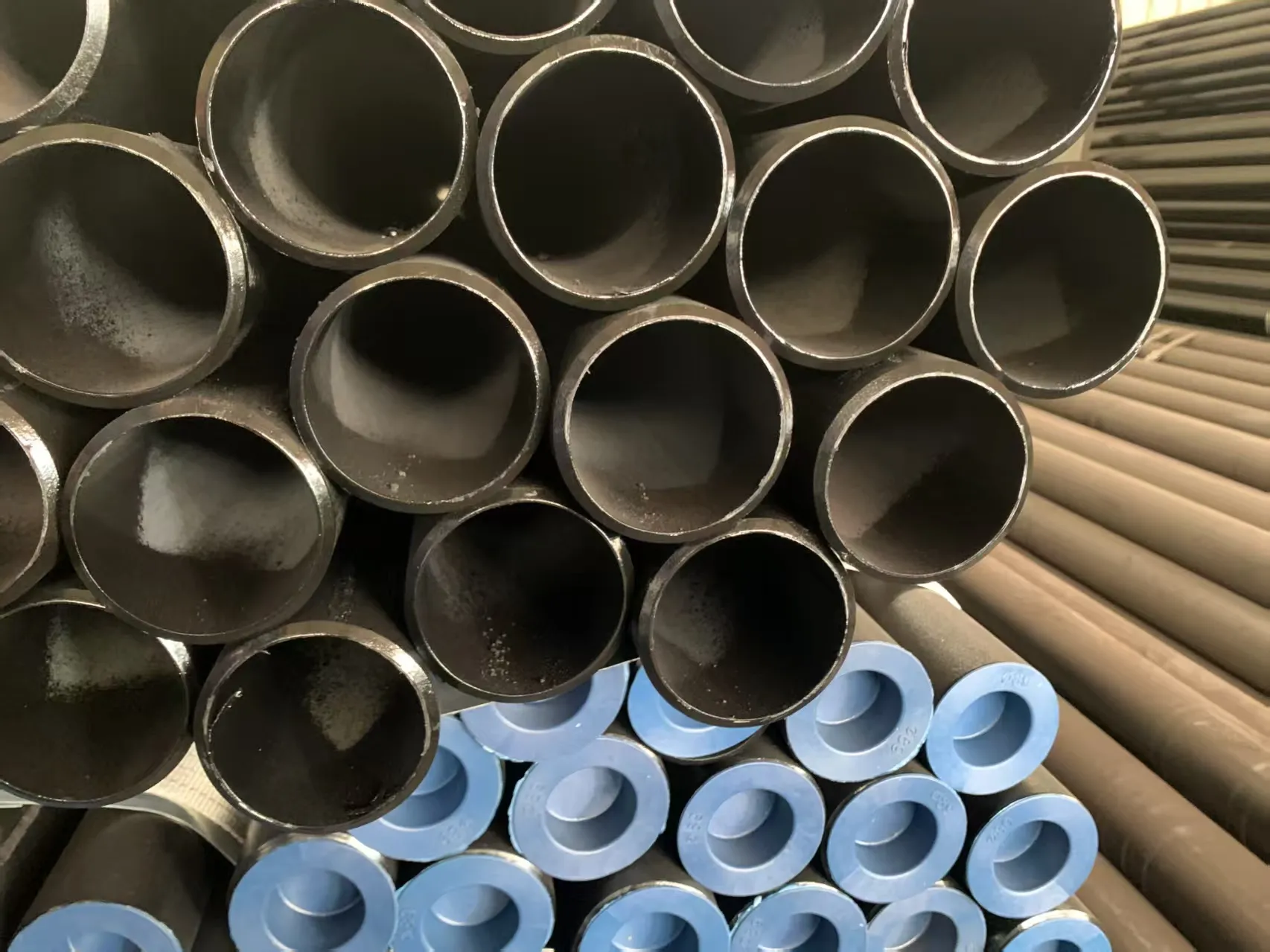
In the realm of industrial piping, flange valves stand out due to their bolted design, which ensures a tight, leak-proof joint. Flange valves are commonly used in situations where the pipe systems require regular disassembly, cleaning, or inspection, as their construction makes them easier to take apart and put together than welded valves. The rigorous standards adhered to in their production—such as ANSI and DIN specifications—testify to their robustness, which provides an authoritative perspective on their reliability.
From an engineer's perspective, there are different types of flange valves, such as gate, globe, ball, and butterfly valves. Each type is designed with specific operations in mind. For example, gate valves operate by lifting a barrier to allow fluid flow and are primarily used where a straight-line flow with minimal restriction is necessary. On the other hand, ball valves provide superior sealing capabilities, featuring a spherical disc to control flow, ideal for high-pressure systems.
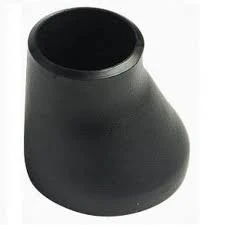
Industry experts often emphasize the advantages of using flange valves over their threaded or welded counterparts. The primary benefit lies in their ease of installation and maintenance. Unlike welded connections which require specialized skills for disassembly, flange connections can be easily unbolted. Additionally, they facilitate quick replacements and upgrades, which is crucial for operations that cannot afford extended downtime.
A crucial component of an optimized operational system is ensuring the appropriate material selection for the valve.
Flange valves come in a variety of materials, including stainless steel, cast iron, and bronze. Engineers must consider the nature of the fluid being controlled, its temperature, and pressure to determine the appropriate material. For instance, stainless steel flange valves are preferred in corrosive environments due to their resistance to rust and corrosion, thereby enhancing the system’s trustworthiness.
flange valve
Prominent manufacturers often furnish flange valves with precision engineering to enhance performance. This includes incorporating seals that prevent leakage and bearings that reduce friction, translating to a longer lifespan for the valve. Quality assurance practices such as hydrostatic testing provide additional trust in their performance, ensuring the valves meet stringent safety and quality standards before reaching the market.
In real-world applications, professionals admire the adaptability of flange valves. In settings such as oil refineries, chemical plants, and power generation facilities, the capability to withstand extreme conditions—like high temperatures and pressures—demonstrates their reliability. This attribute is instrumental in sectors that demand seamless operation around the clock.
Considering the expertise involved in the design and implementation of flange valves, industry stakeholders often consult with specialists to fine-tune their selection. This consultative approach ensures that the specific requirements of an application align with the valve's capacity, material, and design, reinforcing the valve's authoritativeness and reliability in its application.
Moreover, flange valves are increasingly becoming part of the green revolution in industry piping systems. With sustainability becoming a priority, the efficiency and longevity of flange valves play a pivotal role in reducing waste and enhancing energy efficiency. Their ability to be repaired and reused further cements their eco-friendly credentials, lending credibility to industries seeking to lower their carbon footprints.
In conclusion, the technological sophistication and field-tested reliability of flange valves make them indispensable in achieving operational efficiency and safety. Their continued evolution, driven by expert innovation and quality leadership, ensures that flange valves remain at the forefront of fluid handling technology. Whether it is a new build or an upgrade to existing systems, flange valves prove their value through tried-and-tested performance and an unwavering commitment to standards of excellence.