Welding pipe to pipe is a precision-driven task often encountered in various industries ranging from oil and gas pipelines to water distribution systems. Mastering this art requires an understanding of numerous factors that affect the final quality of the weld. Precision in alignment, correct selection of filler material, welding technique, and a keen eye for safety are just a few of the considerations to make the difference between a mediocre and a superior result.
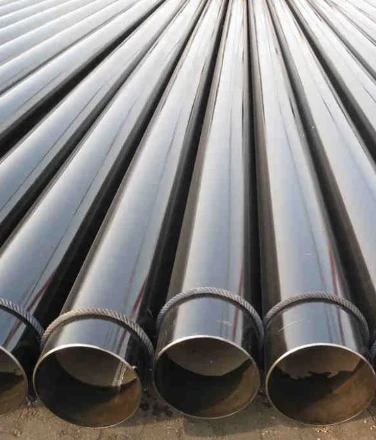
For the weld to be successful, the first step involves meticulous preparation. Begin by properly cleaning the pipe ends to remove any rust, oil, or other contaminants. This step is critical to achieving a strong bond. Measuring and cutting the pipes accurately ensures a snug fit, reducing the likelihood of defects. Ensure the pipes are dry and any necessary pre-heating depending on the material type is done to reduce stress and improve weld penetration.
Selecting the right welding technique is equally crucial. For stainless steel or other heat-sensitive materials, TIG (Tungsten Inert Gas) welding is preferred due to its ability to produce high-quality, precise welds. It allows for better control over the heat input, reducing the risk of corrosion at the weld joint. On the other hand, for general-purpose welding, MIG (Metal Inert Gas) welding might suffice due to its speed and efficiency. Each technique has its benefits and applications depending on the type of pipes being used.
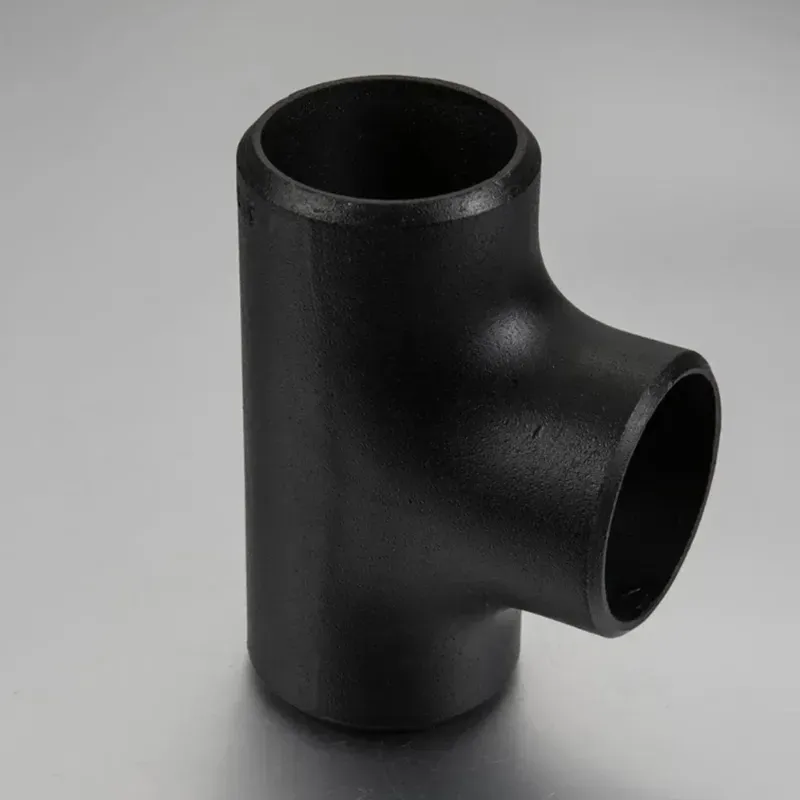
During welding, it's important to maintain consistent power levels to avoid problems like porosity or incomplete penetration. Using a welding clamp or fixture can help keep the pipes in perfect alignment, minimizing gaps that could compromise the weld quality. Movement speed and angle are aspects that cannot be overlooked as they directly influence weld bead formation and joint strength. Routinely inspecting the weld as it's being built provides an opportunity to correct any imperfections early.
The human factor, the technician’s experience, is often the difference between success and failure. An experienced welder intuitively understands the interplay of heat and material, adjusting amperage and speed based on real-time conditions. Their proficiency is backed by certifications that affirm their capability to handle various materials and techniques, ensuring a reliable result that meets industry standards.
pipe to pipe weld
Quality control plays a pivotal role in pipe-to-pipe welding projects. Non-destructive testing (NDT) methods like radiographic or ultrasonic testing ensure the weld integrity without damaging the structure. These tests identify any internal flaws that might not be visible externally but could pose a risk during operation. It is essential to conduct these tests following the welding process to comply with safety regulations and enhance the credibility of the weld.
Trustworthiness in pipe welding also comes from documentation and adherence to welding procedure specifications (WPS). Keeping detailed records of the welding process, materials used, and the testing results creates transparency. In industries where safety and precision are non-negotiable, this accountability fosters trust with clients and stakeholders.
Finally,
safety cannot be underestimated in pipe-to-pipe welding. Protective gear, such as helmets with proper filters, gloves, and fire-resistant clothing, are essential to protect against the high temperatures and ultraviolet light emitted during the process. The work area must be free of flammable materials, and proper ventilation should be ensured to protect the welder from toxic fumes.
In essence, pipe-to-pipe welding demands a balance of expertise, precision, and responsibility. By focusing on experience, technical know-how, and stringent safety protocols, the process can yield durable and reliable joints that stand the test of time. Prioritizing quality and adhering to best practices assures not only the structural integrity of the pipeline but fortifies the reputation of the professionals involved.