Flanges are critical components in a wide array of industrial applications, serving as essential connectors for piping systems. Undoubtedly, any professional involved in industries such as oil and gas, petrochemical, or manufacturing understands the intrinsic values that flanges offer. Capitalizing on decades of cumulative on-ground experience, this composition elucidates the indispensable roles flanges play from a technical and operational standpoint.
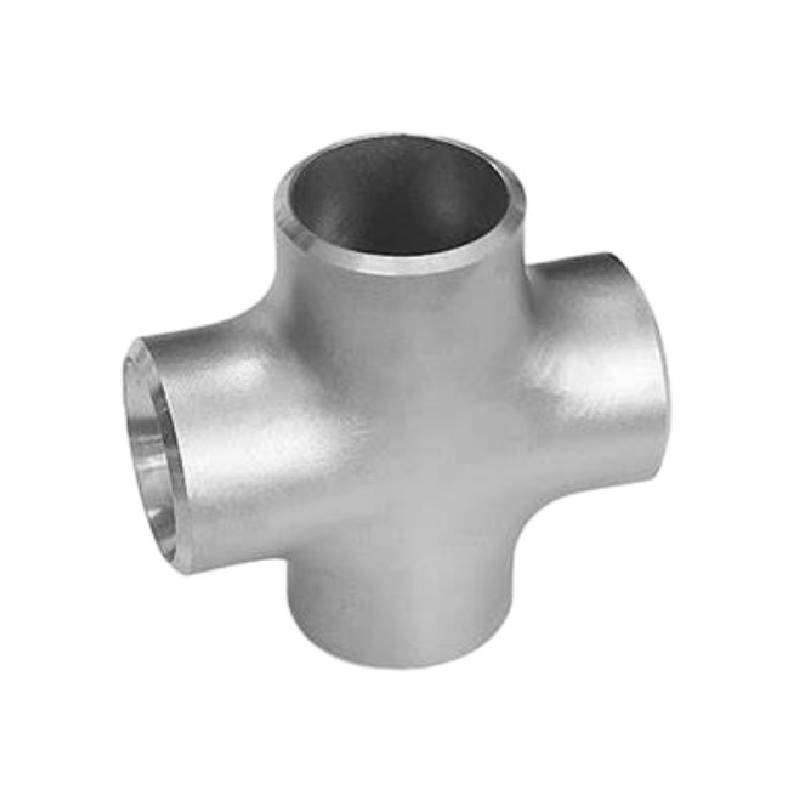
For newcomers and seasoned experts alike, expertise in flange selection can substantially influence the operational efficiency and safety of piping systems. One insightful anecdote recounts a project in the petrochemical industry where choosing the wrong flange type led to catastrophic system failures, underscoring the necessity of profound familiarity and meticulous selection criteria.
In essence, flange systems function on the precise alignment and secure fastening of pipes, valves, pumps, and other equipment, forming watertight containers or channels for the efficient transfer of fluids or gases. The centrality of flanges in facilitating maintenance and inspection further asserts their non-negotiable status in pipeline design and implementation.
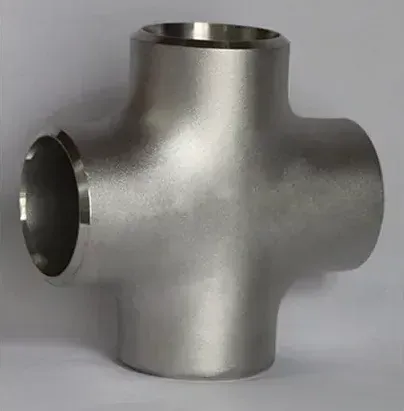
The expertise required in selecting the appropriate flange extends beyond cursory knowledge. One must consider factors such as the type of media to be transported, pressure, temperature, and environmental conditions. More complex variables include the flange’s material composition, usually ranging from carbon steel, stainless steel, to more specialized alloys, and surface finish types, tailored for specific industrial contexts.
Authoritativeness in the domain of flanges can be accredited by understanding standard classifications like ASME (American Society of Mechanical Engineers), BS (British Standard), DIN (Deutsches Institut für Normung), and others. Each standard prescribes specific performance metrics and dimensions, thereby guaranteeing reliability and compatibility in global industrial practices.
1 flange
To establish trustworthiness, the emphasis is placed on rigorous quality assurance processes. Production logs, material test reports, and compliance with international quality certifications build credibility and assure stakeholders of the product’s robustness and service life.
A case study illustrating the application of flanges in a high-pressure application involves the transition from an older flange design to a more advanced design with superior chemical resistance properties. This realignment resulted in fewer maintenance downtimes and enhanced the safety profile of the entire system. Such practical insights are invaluable to professionals seeking to optimize their operational modalities.
True innovation within the flange sector is marked by developments in material science and manufacturing techniques, promoting advancements like flexible design and enhanced pressure ratings. Equally, the advent of smart flanges, integrated with sensors for predictive maintenance, marks a shift toward more sustainable and technologically adept solutions.
In conclusion, maintaining an edge in the ever-evolving industrial landscape requires not just awareness but proactive engagement in acquiring and implementing the latest flange technologies. Experience, expertise, authoritativeness, and trustworthiness collectively underpin what must be a perpetual commitment to excellence in flange applications.
For professionals and industries committed to operational excellence, embracing comprehensive flange knowledge isn’t a mere option—it’s indispensable for fostering long-term success and innovation.